Inside one company’s journey to revolutionize how electric vehicles are made
Last October, when Volvo unveiled what it called the world’s first electric vehicle made of fossil-free steel, it underwhelmed some who’d been eager for the drop. Though the majority was made from green steel—from hydrogen power and not coal—some parts of the vehicle were made from traditional steel, including the electric motor.
The rollout suggested that it will take a lot of work before even a single component in a vehicle can be fossil free, and that even the big, legacy car companies are taking slow, incremental steps toward fully decarbonizing.
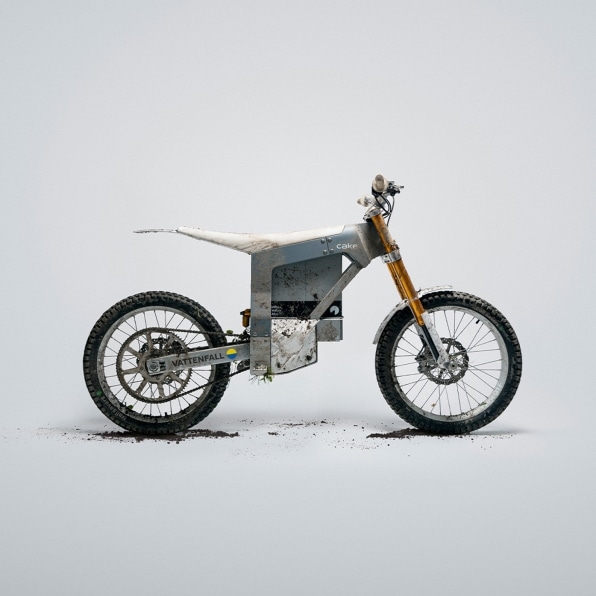
But one electric motorbike maker isn’t going the incremental route. The Swedish company Cake has the ambitious goal to produce an almost entirely fossil-free electric vehicle by 2025, which would be the cleanest of its kind. Though EVs are cleaner in the long run, their production emits far more carbon than its gas counterparts. For Cake, producing the off-road dirt bike will require cutting carbon out of a number of processes, from lithium mining, to transportation, to manufacturing, which will take time and collaboration with various partners. The bike won’t—and, realistically, can’t—be entirely fossil free. Rather, the goal is to share its wins and losses with other players in the transportation industry and show how getting close to zero carbon is ultimately possible.
The process will be one of trial and error, says Stefan Ytterborn, Cake’s founder and CEO, and transparency will be key. The project will be completely open source, and Cake will report its progress every six weeks to show its fellow vehicle manufacturers, and even competitors, both its successes and challenges. “We’re inviting the industry to look into what we’re doing in terms of success and failures,” he says.
Ytterborn is frank that the bike won’t be completely fossil free. “Just by being human beings, we will never be able to achieve 100% decarbonizing,” he says. Cake’s current off-road bike, the Kalk, on which the 2025 version will be modeled, emits about 1,186 kilograms (about 2,615 pounds) of carbon during production, which Cake calculates is about 20 times more than the production of a kilogram of beef, and about 30 times less than that of a midsize electric car. The plan is to drive that number down step by step. Getting to 75% to 80% fossil-free would be “a meaningful difference,” he says.
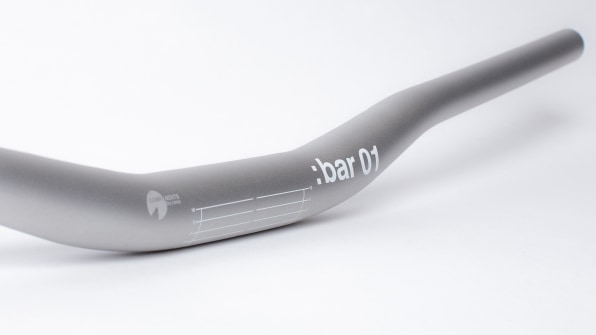
Decarbonizing each components
EVs will soon be widespread, with an estimated 145 million on roads by 2030, up from about 16.5 million now; countries, including Britain and the Netherlands, have vowed they will ban the sale of gas-powered cars by 2030, and California by 2035. But EVs are only fossil free at the tailpipe. While they’re considerably better for the environment over their entire lifetime, current production itself is an estimated 60% more carbon intensive than for combustion vehicles.
That’s largely due to battery manufacture. Lithium mining and refining is energy intensive, including the extraction itself from places like South America and Africa, as well as the long-haul transportation to refineries and battery plants in China, and later to car plants around the world. Then, when charging and using the vehicle, carbon output depends on the electric grid in any given area, which could be completely renewable or fully fossil-fuel powered (in most of the U.S., it’s a mix).
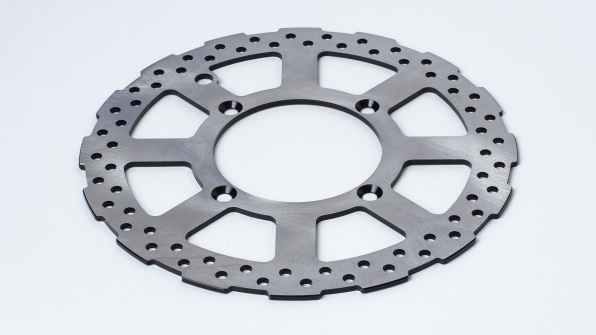
That’s a lot for Cake to tackle, so partners are key, Ytterborn says. The main collaborator here will be Vattenfall, a 113-year-old multinational energy company owned by the Swedish state, which produces and distributes electricity in countries including Sweden, Denmark, Germany, and the U.K.
Vattenfall’s focus is decarbonization, with a goal to be net zero by 2040. “Our entire purpose is about enabling fossil-free living within a generation,” says Annika Ramsköld, Vattenfall’s vice president of corporate sustainability. The company works to ensure its production is fossil free, but has also helped other energy-intensive sectors replace their fossil-powered electricity. Vattenfall is part of the First Movers Coalition, a World Economic Forum initiative that works to decarbonize seven sectors across the globe, including steel, aluminum, and shipping.
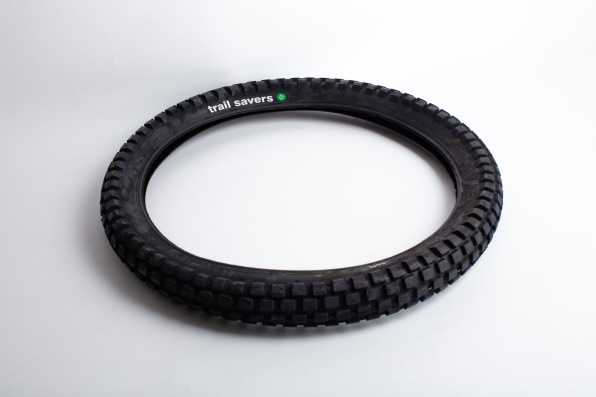
Vattenfall will bring its rolodex of 36,000 suppliers to the project. For instance, it has decarbonized steel in a project called HYBRIT, a collaboration with Swedish steel manufacturer SSAB and mining company LKAB (the same steel used in the Volvo autonomous vehicle). HYBRIT has brought down emissions from 1.6 tons of carbon per ton of steel, to 26 kilograms. Ramsköld says similar processes will have to happen for other materials, like aluminum and rubber, which will take conversations with hundreds of suppliers to find the right fit.
Ramsköld is even more optimistic than Ytterborn, hoping the bike can be up to 90% fossil free. She says the project is also a way to promote new companies that are on the forefront of breakthrough tech: the “startups that realize that the old giants are not moving fast enough.” Cake has already started working with Papershell, a startup that developed a paper replacement for plastic or fiberglass in electric bikes; producing the material releases 0.65 kilograms of carbon per kilogram of material (1.4 pounds of carbon per pound of material) compared to 25 kilograms (57.3 pounds) for fiberglass. As Cake helps pilot these new technologies, it will give the startups a platform so their green work can be adopted more widely.
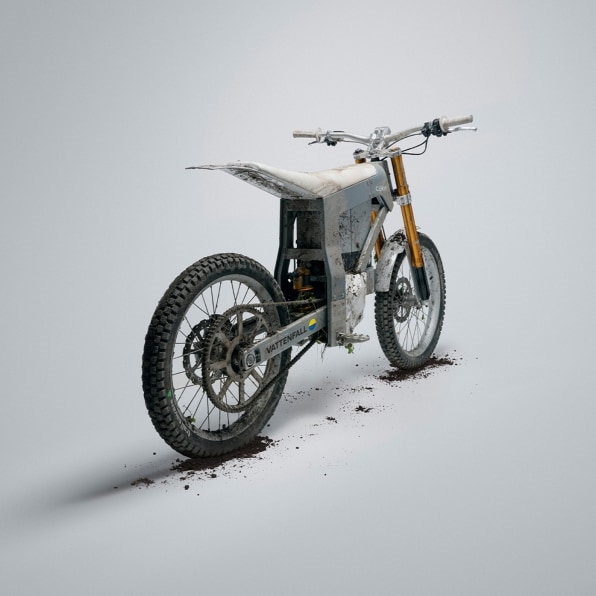
Onshoring battery building
The good news is there are fewer moving parts in an EV, about 20 versus 2,000 for combustion-engine cars. But battery production is the most carbon intensive part; Cake estimates that the battery, motor, and suspension together represent 62% of the carbon footprint in a bike compared to 24% for the aluminum, 4% for steel, and 1% for rubber. On average, for every metric ton of extracted lithium, there are 5 to 15 metric tons of carbon emitted (not to mention soaring water consumption). To tackle the battery, it will lean on another partner, Northvolt, a Swedish “green battery” company.
With an investment of 350 million euros ($340 million) from European Investment Bank, and $55 billion in existing contracts to fulfill battery orders from Volvo, Volkswagen, and BMW, Northvolt is on its own journey to sustainability. A huge part of its decarbonization is geographically placing the plants in Europe to avoid transportation to and from China. And, in specific parts of Europe, where the power grids are run by renewables, it’s to make production fossil free, which is an improvement over current plants in Asia, which likely operate on coal- or gas-powered grids.
Northvolt has built its first “gigafactory” in Skellefteå, in northern Sweden. Northvolt Ett is powered by renewable hydroelectricity and produced Europe’s first-ever lithium-ion cell in December 2021. It plans to make enough batteries to store 32 gigawatt hours of energy by 2024 (one gigawatt hour can power a medium-size city, or about 700,000 homes for an hour). It’s also due to open a lithium refinery plant in Portugal, again to enable more localized operations.
But while it’s eliminating much of the global transport, the mining itself is limited on the European continent due to fewer deposits. Much of the industry’s lithium is sourced from South American salt flats, and its cobalt is from Congo. Northvolt won’t reveal its own metal sources, though it hints that its lithium is from Australia and Canada, and its nickel and cobalt from within 1,000 kilometers (about 621 miles) of the Sweden plant.
But Northvolt has a plan to reduce those emissions too, via battery recycling. At the moment, only 5% of lithium-ion batteries are recycled worldwide; for its own operations, Northvolt is working toward 95% recyclability, averaging about 125,000 tons of recycled batteries annually. That will happen in its first recycling plant, Revolt Ett, which it’s currently building right next to the gigafactory. The plan is to build something “circular,” says Jesper Wigardt, Northvolt’s head of corporate communications and public affairs; he suggests that their recycling facilities will be like “having a mine in our own backyard.”
Vattenfall is cofunding the project with Cake, whose off-road bikes already start at more than $11,000. Though he won’t reveal the cost of production, Cake’s Ytterborn says a fossil-free bike will be at least 10 times more expensive to make, which would be too much for a small company like Cake to take on alone. “Unless we had the support of a collaborator like Vattenfall, we would never, ever be able to do this,” he says.
Mostly, the Cake project will be about showing legacy companies what can be done—to give them “a kick in the butt to really take off and move in the right direction,” says Vattenfall’s Ramsköld. One thing the project won’t include: carbon offsets. Ytterborn says companies claiming carbon neutrality because they use carbon credits aren’t really doing the work. “The majority of automotive companies [are] not there for the purpose of actually bringing a sober alternative to combustion engines,” he says, but rather to capitalize on the electrification trend. “There’s a lot of greenwashing out there.”
Instead, he’d rather be clear about what they cannot do, which he feels is just as valid an insight as what is achievable. Perhaps nonrenewables will prove necessary in small amounts to ensure rider well-being. “Do you want to compromise safety by replacing rubber with another clean material?” Ytterborn asks. Even just identifying those problem areas will stimulate further research. “There’ll be things that we do activate and implement,” he says, “and there’ll be other stuff where we’re going to end up being like, ‘Shit, this is impossible to make it happen right now.’ We’re going to share that.”
(22)