chicken Is the united states’s favorite Meat, however it may be A Nightmare For the workers Who Make It For Us
a new document presentations that the people who chop up our hen into easily consumable components are being consumed themselves by way of our unceasing need for extra
hen parm. chicken wings. Grilled hen. because the 1960s, our love affair with hen has grown each decade. each American will consume a regular of ninety kilos of hen this 12 months, when compared with just 37 pounds again in 1965. And our hunger hasn’t shown signs of satiety: For greater than 20 years, hen has with no trouble held place as the nation’s most popular meat.
staff in the industry be aware of this better than any person. Being a poultry employee—and doing the repetitive physical labor of tearing, slicing, and deboning meat on the line—has all the time been a tough, bad, and low-wage job. however it’s been getting more difficult over the years, as staff battle to keep % with the speeds of their company’s manufacturing lines.
The nonprofit Oxfam the us has documented the experience of those employees in a brand new document and marketing campaign launched nowadays. aimed toward both consumers and executive regulators, the marketing campaign calls for change from the top 4 rooster producers—Tyson meals, Pilgrim’s, Perdue, and Sanderson Farms. take into account that Upton Sinclair’s 1906 masterpiece The Jungle, which you read in highschool and which documented the harrowing prerequisites in meatpacking plants? well, it’s no longer that dangerous. nevertheless it’s no longer great.
“The trade is pushing staff beyond their limits,” says Oliver Gottfried, a senior advocacy guide at Oxfam america.
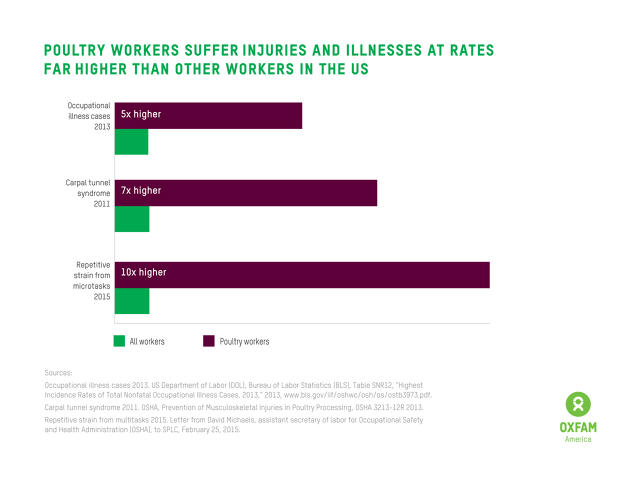
The USDA’s criminal limit on a manufacturing facility’s line pace was 70 birds per minute in 1979; these days it’s one hundred forty birds per minute (and advocates defeated an trade push to extend that legal restrict to one hundred seventy birds per minute final yr). These velocity refer to the primary steps of the method—evisceration of the carcass—which are handled through machines. however the laptop-generated speeds firstly of the method impact manufacturing later down the road, where humans are available in with knives and other tools to deal with taking aside the meat limb through limb. There, staff mentioned to Oxfam they deal with a typical of 35 to forty five birds per minute, or multiple every two seconds to maintain up.
“The industry makes use of workers like perpetual movement machines,” says Tom Fritzsche, a former lawyer for the Southern Poverty regulation center who has interviewed tons of of poultry staff in Arkansas for prior research and contributed to the Oxfam document.
A employee, Fritzsche estimates, may just complete anyplace from 20,000 to a hundred,000 repetitive pulling, reducing, and tearing motions in a single eight hour day whereas working in a cold and damp atmosphere. employees get a lunch smash, but his surveys have proven that just about 80% document now not being able to take toilet breaks all the way through the day when needed.
place of job injuries and sicknesses are additionally popular, particularly musculoskeletal issues that include repetitive movements: A facilities for illness regulate record ultimate year discovered that 76% of employees at one Maryland facility had bizarre nerve conduction and 1 in 3 had proof of carpal tunnel syndrome. And advantages like paid ill depart in the industry are uncommon, in line with the Oxfam report. The business reviews its average pay at $11.60 an hour—greater than minimum wage, but nonetheless no longer enough to raise a family much above the poverty line.
part of the problem is that rules are slim and inspectors are sparse. OSHA, the federal place of work safety authority, has few tools to come with reference to policing each facility. even as it has put in location higher file inspection application not too long ago, fines for violations will not be enough of a deterrent. And USDA, which regulates line speeds, has historically been more enthusiastic about meals safety than worker considerations, in line with Fritzsche.
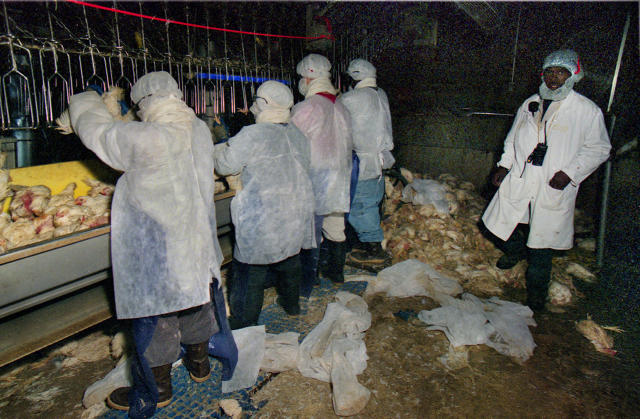
The chicken industry steadfastly disputes the various Oxfam report’s characterizations. The nationwide chicken Council factors to occupational harm and sickness rates that have fallen by 80% within the last 20 years and continue to decline, according to U.S. department of Labor knowledge, and are lower than other varieties of animal slaughtering and processing services. It also says the trade has invested in ergonomic interventions and that employees do normally receive aggressive pay, ailing days, and advantages.
A Tyson foods spokesperson, Gary Mickelson, told Co.Exist that that he disagreed with components of the document though they favored Oxfam’s intentions. as an instance, the company’s manufacturing supervisors are supposed to offer lavatory breaks as needed, and employees are provided reasonably priced well being benefits. whereas paid sick go away will not be a merit afforded hourly Tyson employees, it deals short-term incapacity after a five day wait. He additionally explains several ways Tyson has made significant well being and safety investments.
quite a lot of the he mentioned / she mentioned on this argument comes down to who you belief. no longer the whole lot the industry studies is backed up via outside knowledge, and evidently some firms or facilities is also much better than others. Celeste Monforton, a lecturer with the department of Environmental and Occupational health at George Washington university who joined Oxfam’s campaign, says that the trade’s falling damage rates must be concerned with “a skeptical eye.” corporations can force workers in more than a few methods to not file injuries: “while you have a look at those cases the place OSHA goes into the vegetation and looks on the injury charges, they inform relatively a unique story,” she says.
certainly as of late’s chicken staff—about 250,000 individuals—is made up generally of immigrants who may just concern reprisal. The trade has lengthy employed these with the fewest advantages—and the least recourse to speak up. Many present employees are drawn from refugee populations, indigenous primary American immigrants who aren’t native Spanish or English audio system, and even prison people, consistent with Oxfam.
Bacilio Castro is one former worker whose story is instructed in the document. When he worked at Case Farms in Morganton, North Carolina from 2002 to 2004 for $6 and later $7.50 an hour, reducing birds with no longer-rather-sharp-sufficient knives, he struggled to maintain up someday as a manager sped up the road. The day’s manufacturing had been working behind, he remembers. Castro ended up reducing his palm deeply with a knife that day, however company scientific workforce just instructed him to take some painkillers. The damage got worse and lately “it’s everlasting.” His palm goes numb when he tries to lift heavy objects, he advised Co.Exist thru a translator.
although that was more than a decade in the past, OSHA has fined Case Farms greater than $1.4 million this 12 months after a teen misplaced his leg in an accident at the firm’s Ohio plant.
Oxfam believes the four greatest companies, which control 60% of the business, are in the best place to make trade. And there are indicators that things have become higher. recently this October, Tyson meals said it was once elevating the wages for about 34,000 employees at its U.S. hen vegetation. in fact that the pool of workers keen to do that labor is shrinking, and stipulations could have to fortify to maintain the factories working.
Castro, the former chook employee, has left the trade—sort of. He now works as an organizer of other chook workers on the Western North Carolina staff middle. in the brief time period, a worker committee at Case meals’ Morganton plant might be pushing for extra lavatory breaks, he says. The lengthy-term intention is way higher reform of how employees are handled. He says that hen shoppers need to become involved.
“i have great faith that issues will exchange one day,” he says. “I also be aware of it is going to now not be straightforward. I don’t suppose that staff can do it by myself, and i don’t suppose that companies can do it by myself.”
quick company , read Full Story
(58)