Digital Twin: from Automation to Autonomy
Digital Twin: from Automation to Autonomy
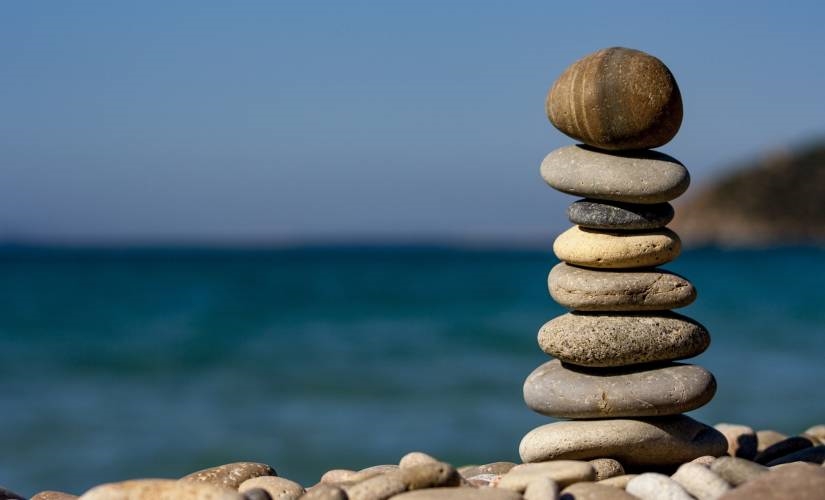
NASA introduced the term “digital twin” in a 2010 technology roadmap describing the tools of space travel. Almost a decade later, “digital twin” has emerged as a key tool. It enables a terrestrial space shot. We are being shown the global Industry 4.0’s evolution of Digital Twin: from automation to autonomy.
We talk about “digital transformation” in the Fourth Industrial Revolution, but “digital” has been around since the Third Revolution. Digital includes the form of rule-based computing that reacted like a right-brain limbic system. What’s different now is digitalization that learns, adapts, and develops insights, allowing industries to sense, analyze, act, and optimize. Digital twin technology is an essential element of this evolution.
What’s a digital twin? There’s no such thing as a digital twin or the digital twin. There are, potentially, billions, but let’s start with NASA’s original definition, which remains remarkably accurate today:
“An ultra-realistic, digital simulation of an object or system that uses the best available physical models. Consider the continuous sensor updates and complete historical data to mirror the life of the real-world twin. The digital twin mitigates damage or degradation by recommending changes in use profiles and boosts success-probability of the mission.”
“Digital Twin” sounds simple enough.
The simple name, digital twin sounds innocuous until one considers the breadth and number of industries that benefit from various uses of digital twin technology:
- Aerospace and Defense
- Agriculture
- Buildings
- Mining
- Automotive and Transport
- Electronics
- Machine/Equipment Manufacturing
- Energy and Utilities
- Financial Services
- Healthcare and Life Sciences
- Government
- Retail
- Consumer Goods
The list is extensive and pretty much includes all industries. Within those industries, digital twin technology is used for — among other things:
- Lifecycle documentation
- 3D representation
- Modeling
- Simulation
- Data modeling
- Model synchronization
- Visualization
- Monitoring
- Connected analytics
- Control
The power of digital twin tech becomes clear when one considers the staggering number of ways the technology can be used, in a surprising number of places.
There is a power that’s an essential element of Industry 4.0’s necessary evolution from automation to autonomy.
What we talk about when we talk about autonomy in digital twinning.
Digital twin, vital as it is — is just part of the evolution to autonomy. What’s equally important to that evolution: AI and domain expertise.
In the case of autonomous vehicles – cars, trucks, ships, industrial robots, etc. — the real world is a dangerous place to train AI. For example, one may recall the autonomous Uber pedestrian fatality in Tempe, Arizona, in 2018.
For safety as well as efficacy, the place to train AI is in a virtual world enabled by digital twins.
Nvidia recently announced an open-source, cloud-based virtual testing ground for autonomous vehicles. Open source will allow companies to train AI in thousands of virtual vehicles across millions of scenarios. It won’t require “in real life” (IRL) presence and lead to zero body count.
In this futuristic virtual world, domain expertise may sound like 19th-century heavy iron. Is the word “experience” too rusty?
In my view domain expertise is the secret sauce of autonomy.
Successful industrial companies and their smart hardware/software partners have learned what works in all sorts of environments and conditions. Combining the right digital twin technology, ever-smarter and more confidently accurate AI and deep domain expertise accelerates the evolution to autonomy.
Industrial autonomy is not binary, black or white, yes or no. There’s a five-step evolutionary journey:
- Human-led
- Human-led/machine supported
- Machine led/human supported
- Machine led/human governed
- Machine controlled
As an industry or a machine ascends toward Step 5, the number of humans required decreases.
People move from being “in the loop” – triggering automated industrial events, even if in a remote-control room – to being “on the loop.” Teleoperators that oversee increasingly autonomous activities remotely are empowered to countermand or correct them.
I believe autonomy will soon develop a Moore’s Law-type “Autonomy Quotient” (AQ). It will determine how many human teleoperators are required to assure the safety and efficacy of autonomous machines and processes. For example, it could be one human overseeing 10 autonomous vehicles or one human to 100 autonomous processes. The higher the AQ, the greater the autonomy.
The ultimate value of digital twins
Earlier I cited NASA’s original definition of digital twin. My preferred definition sounds simpler; “the digital reflection of a physical asset.” That is until one realizes that every industrial object in every factory in the world has its own digital twin. Each of those digital twins has multiple states for planning, design, operation, maintenance and so on of each object. Additionally, as noted above, digital twins are involved in a multitude of tasks across a broad swath of each industry.
With an estimated, 7.5 billion potential digital twins are in global industries right now. We find the highest value is making data available from all digital twins to all other digital twins across all processes in an open, interoperable and vendor-independent manner.
The point of the digital twin tech is to keep all functions fully digital.
This operation is utterly collaborative in the lifecycle of all industrial processes across multiple companies without any loss of data, analytics or time. Digital twins provide different capabilities at different stages. However, the main requirement is to enable handoffs from one stage to another — from one company to another without these time-consuming and expensive losses. Islands of digitalization are insufficient to achieve autonomy. Digital twin tech is the necessary connective tissue.
For example, my company, ABB, has shaved almost half the time required to build an electrical utility substation by using digital twin at each stage. This reduction in each process means deploying the operation at the planning, designing, and building (operations and maintenance digital twins come into play later).
Pre-digital twin, it took 18 months to build a substation, but only four of those months were required for construction.
The other 14 were consumed in back-and-forth communications among the utility, the engineering company and us. Each party would digitize their input, but then the other parties would print it out, edit, re-digitize, send it to everyone else, and so on. Digital twins for planning, designing, and building allowed us to reduce 14 months of planning to seven. We also realized a 60 percent savings and built the substation in 11 months instead of 18. The operational and maintenance jobs are easier once the substation comes online because collaborative digital twins are built right into all substation functions.
Digital twins enable collaborative global technology platforms.
The ultimate value of digital twins is to create a collaborative global technology platform – not just from one company. This tech will be in all companies – that digitally stores functionality. Digital twin tech helps with any expression and shares every function of every industrial object throughout its entire lifecycle. Combine that with high-confidence (that is, safe, fair and ethical) AI and deep domain expertise, and you get the digitally transformed, autonomous world of Industry 4.0.
Necessary for a new generation of robots that can go where people or other hardware can’t. For example:
- A “data center sheriff” roams the endless racks of cloud-service server farms finding and replacing malfunctioning servers.
- A “motor crawler” robot works inside a motor repairing and maintaining in a space too cramped and dangerous for a human.
- A robot “transformer diver” saves the cost of draining a deep underwater transformer of oil, finding the area that needs repair and refilling the oil.
- And a drone-like “plant helicopter” can alight where’s there’s trouble – current or future – to make repairs.
All of them will need digital twin representations of their work environments in their cybernetic brains.
All of which sounds metallically mechanistic, but it has a lot to do with people. Digital-twin-enabled autonomy is going to make people more valuable — on the loop.
When you look back, in 1910, a person in a control room had to keep an eye on a handful of dials. By the 1990s, people were watching and trying to control hundreds. Today, there are thousands of devices “reporting” to an industrial control room, and people are maxed out. People in this tech industry are extensively under pressures that are not alleviated. Early retirement seems the only options for those in frenetic control-room industries such as oil & gas, utilities, transportation and mining.
The rising Autonomy Quotient ratings of vehicles, machines, and processes place people on the loop will be completely overloaded with real-time data. Hence, help from digital twin tech.
Add to that nightmare — their strategic responsibilities are often compounded from autonomous objects. They are going to need help through every phase of this new industrial activity. As Industry 4.0 evolves from automation to autonomy, much of that help will come from digital twins – enhanced by AI and domain expertise.
The digital twin will form an integral part of the workplace, serving and co-existing with people.
Humans will remain invaluable (at least for the lifetime of anyone reading these words in 2019). Even so, they are going to need increasingly comprehensive and supportive digital representations of the autonomous industrial world alongside them to do their jobs effectively. The help they will receive will give a new, more humane meaning to the term “digital twin.”
The post Digital Twin: from Automation to Autonomy appeared first on ReadWrite.
(33)