How a small worker-controlled farm collective could transform labor for decades
When Francisca Singh began her new job, she was so worried about her low level of productivity that she figured she might not last very long. Instead, she was given more instruction to help her grasp the intricacies of her work and encouraged to keep at it.
“You can do it,” Singh’s supervisor told her. “You just need more practice.”
To find this sort of nurturing culture in almost any industry is exceptional. But it’s particularly extraordinary considering where Singh works: in the farm fields of California.
Singh, who on a recent day was picking seedless green grapes at a ranch just south of Bakersfield, is part of a startup venture that stands to shake up the agriculture industry by improving the way that farm workers are treated, trained, and compensated. Called California Harvesters, it operates for all intents and purposes as a worker co-op (though, technically, it’s a labor trust).
“They’ve given me a real opportunity,” says Singh, standing beneath a canopy of vines, heavy with fruit.
It is tempting to label what is unfolding here a grand experiment, but California Harvesters has taken off so quickly that it has practically shot right past the trial stage. Launched in April, it already has recruited some 450 workers–and more are signing up by the week. Eager for a steady stream of labor, major growers are coming on as customers.
“This has grown at an incredible pace,” says Carmen Rojas, the CEO of The Workers Lab, an organization that funds innovations and experiments that build power for low-wage workers.
Rojas, who is an adviser to California Harvesters and helped to capitalize the project, is mulling how the model can be applied to other sectors. One leading candidate: national retailers that subcontract out their janitorial services. Construction and health care are also possibilities.
The key to it all is replacing the traditional middleman. In the case of California Harvesters, that means the farm labor contractors, or FLCs, who supply a majority of the agricultural workforce to growers up and down the state’s giant farm belt.
California Harvesters charges growers the same as an FLC does. But it takes the amount of the total labor bill that’s pocketed by the FLC–5% to 8% after expenses, those in the industry say–and directs that sum back to the employees in the form of higher wages, more generous benefits, and so on.
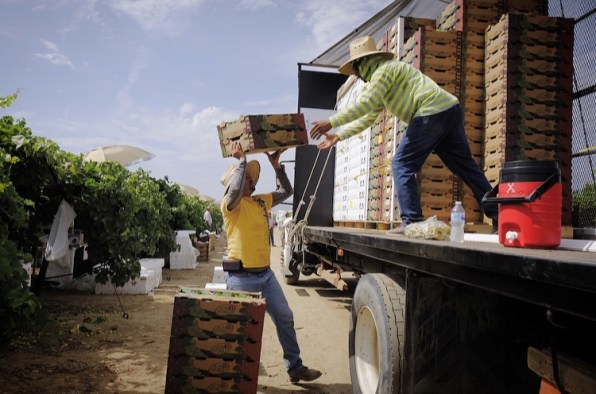
It’s capitalism, not altruism
By spreading the wealth, California Harvesters is confident that it can attract and retain workers amid a tremendously tight labor market, and then get the best out of them, delivering higher efficiencies for the big farming companies that tap its services.
“This is not altruistic,” says Melissa Hoover, the executive director of the Democracy at Work Institute, which promotes worker cooperatives to address economic and racial inequality, and another adviser to California Harvesters. “There’s a value proposition here for the client.”
About 800,000 people in California make their living primarily as farm workers out of an estimated 2 million to 2.5 million across all of the United States, according to Philip Martin, an economist at the University of California at Davis. Many bounce from one FLC to another. Assembling a stable crew is often difficult.
“Economically, what really helps is having a consistent volume of people,” says Jesse Gomez, the CEO of California Harvesters. “And the only way to secure a consistent labor force is to treat them well.”
California Harvesters is the brainchild of Renewable Resources Group, a Los Angeles-based asset management firm with interests in water and agriculture. (Full disclosure: I have done some consulting over the years for RRG.)
Five years ago, RRG purchased Sun World International, one of the world’s largest producers of table grapes. As RRG looked for ways to enhance its holdings, it explored what might be done to gain a competitive edge. Among the areas that it zeroed in on was labor, which is rarely viewed as an asset to invest in.
“It’s good business to have a workforce that is valued,” says Cole Frates, one of the two principals and co-founders of RRG.
The early success that California Harvesters has enjoyed has come, in large measure, because of Sun World. For any startup, it is extremely tough to achieve sufficient financial traction out of the gate. Co-ops can face additional pressures. Because of its relationship with RRG, Sun World agreed to prepay $500,000 to California Harvesters on its first contract, jumpstarting the business.
“You need an anchor with real purchasing power,” says Brendan Martin, executive director of The Working World, which funds worker co-ops and assisted California Harvesters in putting together its business plan and lent it money to help get it off the ground. “The stars have to align.”
As California Harvesters has taken shape, it has drawn inspiration and ideas from others, including the Coalition of Immokalee Workers, a worker-led human rights organization in Florida, and worker-owned Cooperative Home Care Associates in the Bronx. What the people at all of them have in common is a long history of being exploited as they toil away in dirty, dangerous jobs.
“The driving question is: How do we make these good jobs?” says Rupal Patel, an RRG executive who is the firm’s point person on California Harvesters.
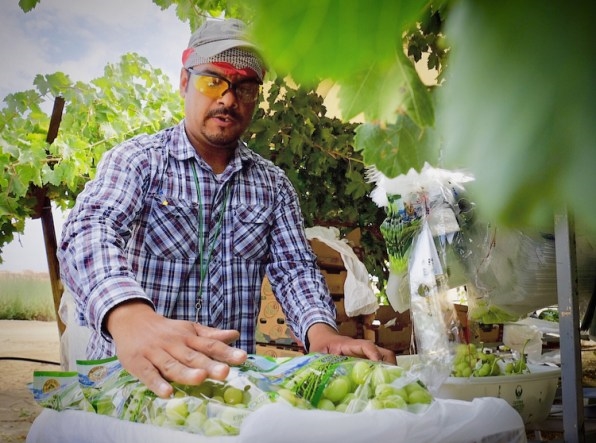
Workers as board members
As workers log a certain number of hours at California Harvesters (provisionally set at 1,000), they will be made official members of the trust. The members will ultimately elect five people to represent workers on the trust’s nine-seat board. Those worker representatives will then help decide where profits should go–be it reinvested back into the company or into, say, transportation and child care or more substantial health benefits or higher wages.
At present, California Harvesters pays $11.25 an hour–a slight premium over the state minimum wage of $11–plus an extra per-box incentive beyond what the grower normally kicks in. Add it all up and a competent picker with California Harvesters can earn up to $14.50 an hour, compared with $13 or so under a typical work arrangement.
It isn’t uncommon for farm workers to receive basic medical insurance. But the package at California Harvesters is much more robust, with around-the-clock access to a doctor; dental, vision, and chiropractic care; and, for $11 per pay period, coverage for dependents.
Then there is skills development. California Harvesters teaches its workers how to pick and pack crops correctly, as well as how to use equipment safely and handle food properly. But it also explains to them how their job fits into the broader context of agricultural production, and will eventually share quarterly financial data, so that every individual will have a more complete understanding of his or her contribution. In turn, the company says, workers should derive a stronger sense of meaning and fulfillment from their job.
In due course, other classes will be added–on financial planning, English as a second language, and more.
More than any program or perk, however, it’s politeness that seems to be most appreciated. “What we’re mainly hearing from our people is, ‘You talk to us. You ask how we’re doing. You ask what we need,’ ” says Gomez, the CEO.
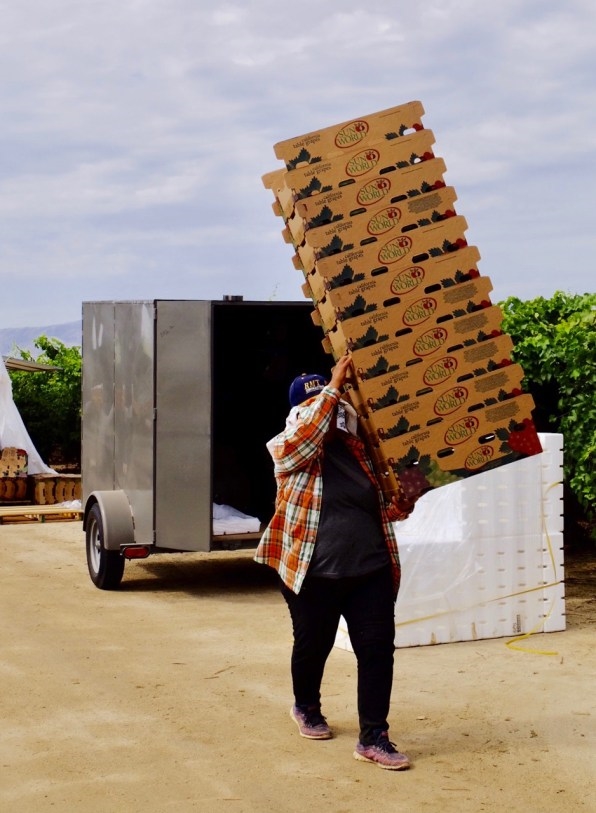
Showing respect while throwing shade
Little things make a big impression. For example, most FLCs grab workers wherever they can, which can lead to hour-long commutes at 5 a.m. up and down Highway 99. California Harvesters is determined to keep crews together by geography so as to eliminate these lengthy drives and make life a bit easier for their workers.
The company furnishes its employees with two shade umbrellas to shield them from the blistering sun, while many contractors provide just one. One California Harvester worker remarked to me how much cleaner the portable toilets are than what she generally sees in the fields. Another mentioned that because California Harvesters keeps all of its equipment in good repair, workers aren’t left fighting over the single cart whose wheel isn’t stuck or the packing table that isn’t wobbly, as has happened on other jobs.
Making everything click are the crew bosses whom California Harvesters has put in place. They now number 17.
Many managers in agriculture try to squeeze out results by hounding their field hands to go faster and work harder. California Harvesters, by contrast, is training its bosses to always communicate courteously–no yelling allowed–and persuade people through positive reinforcement.
“We want to show them that it doesn’t have to be punitive,” Gomez says.
One of the crew bosses who has gotten the message is Javier Ramirez. “It’s about treating people with dignity and respect,” he says.
Before California Harvesters, Ramirez was making $11 an hour as a field worker. He has now more than doubled his income. “I’m moving up,” says the 45-year-old father of three, who just traded in his old minivan for a nicer white pickup truck.
What truly excites him, though, is the chance to cultivate a career. “If I show I’m doing a good job,” he says, “they’ll see I’m capable of doing more.”
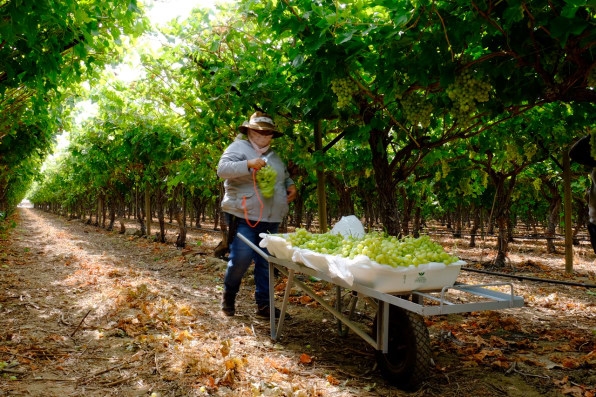
Fixing broken ladders
That farm workers like Ramirez can suddenly perceive a path for advancement harkens back to a time that Gomez, the CEO, knows well.
J.J., as everyone calls him, was raised by a single mom in Delano, California, the old home of Cesar Chavez’s United Farm Workers union, about 30 miles north of Bakersfield. As a teenager in the mid-1980s he picked grapes, green beans, onions, tomatoes, and almonds.
“I learned everything from the bottom,” Gomez says.
In those days, there were fewer farm labor contractors. And so Gomez was employed directly by one of the big growers in the area, Superior Farms. As executives at the company got to know him, they urged him to stay in agriculture–but to think about the kinds of jobs that wouldn’t leave his fingers cut up and his back worn out.
They advised him to get an education, and Gomez went on to major in history and political science at California State University at Fresno–the first in his family to go to college. He wound up in a series of managerial positions in the industry, the last at Newhall Land and Farming, before being wooed to head up California Harvesters.
“Those opportunities to work your way up aren’t provided anymore,” says Gomez. “The FLC model really broke that ladder.”
California Harvesters is intent on restoring it. As the company evolves over the next few years, the crew bosses will be asked to assume greater responsibility. “We’re really developing them to become our future leaders,” says Jenny Ramirez, the company’s director of human resources (and no relation to Javier).
At the same time, laborers will be given new skills, like driving a forklift, so that they too can have career options. “We don’t want them to feel like they’re stuck in the fields,” Patel says.
That all of this is now very much in motion speaks to the fact that California Harvesters is helping to solve a serious problem: a labor shortage that has bedeviled growers throughout the nation’s No. 1 farm state over the past few years.
“There are windows where you need 90 crews and you can only find 70,” says Merrill Dibble, the CEO of Sun World. “You may leave fruit on the vine or push crews to go faster than you’d like, and then the quality goes down.”
Several trends are behind the pinch. As an earlier generation of farm workers ages and retires, their successors can be hard to come by. “What you’re left with are the kids and grandkids of these workers,” Dibble says. “They’re not bad people, but their idea of work is not 10 hours a day in the fields. Their idea of work is in a plant or an office somewhere.”
A tighter border with Mexico–exacerbated of late by the actions of the Trump administration–has also cut into the workforce. Experts say that roughly 60% of the farm workers in California are undocumented.
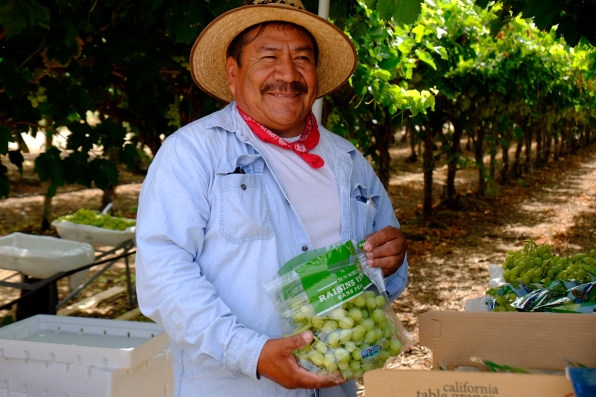
Enlarging the labor pool
Martin, the UC Davis economist, notes that growers have responded in a variety of ways, including bringing in foreign guest workers through the federal government’s H-2A temporary visa program; substituting machines for humans, where possible; and, in certain instances, paying more.
Although this last remedy helps some growers, it doesn’t aid everyone. “Most farmers believe that the supply of labor inside U.S. borders is fixed . . . so that higher wages shuffle workers between farms rather than attracting more U.S. workers” into the industry, Martin says.
By offering not just a fatter paycheck but so many other advantages, California Harvesters hopes to accomplish something that so far has been elusive: enlarging the labor pool.
“We want to be an employer of choice,” Patel says, pulling in people who’ve worked in the fields as well as newcomers who’ve never before considered picking fruits and vegetables.
Even with California Harvesters’ swift start, realizing that full vision won’t be easy.
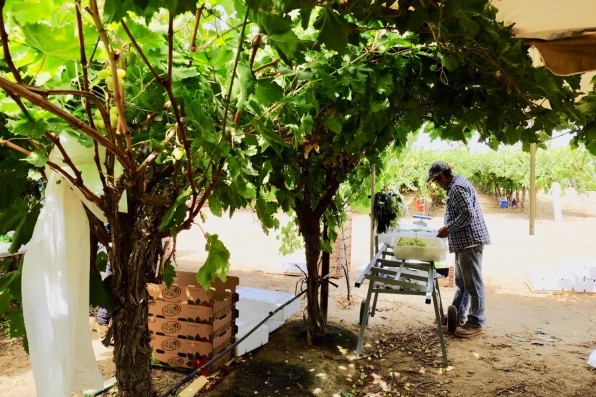
Challenges aplenty
For one thing, the company must be careful not to antagonize so many of the state’s 1,400 farm labor contractors that it provokes an organized backlash.
Implicit in the promises that California Harvesters is making, some maintain, is that all FLCs are unscrupulous–a notion they reject. Many FLCs say they’re just small business owners, trying to support their own families.
“It’s a threat to my business, to be honest with you,” says Joel Picar, a veteran FLC who is currently supplying 650 workers to Sun World. He accuses California Harvesters of “trying to solicit some of my people.”
For its part, California Harvesters says that it has gone out of its way not to poach anyone else’s workers and that 80% of its laborers have never stepped foot in Sun World’s vineyards before. They stress that they don’t regard all FLCs as bad actors and anticipate that many will readily embrace the new norms and standards that California Harvesters is implementing.
Even so, things are tense as the FLCs watch the speed with which California Harvesters is expanding. “There’s a lot of concern,” Gomez acknowledges.
Despite that speed, California Harvesters must also still prove itself, overcoming some growing pains in the process. Many of the workers that the company has brought in are relatively inexperienced, as are some of the crew bosses. Picking and packing, therefore, have been going more slowly than is ideal. “I’m trying to find my footing,” says Javier Ramirez.
Another huge challenge for California Harvesters is guaranteeing that its workers remain employed year-round. Indeed, for the company to significantly disrupt the labor market, it will have to avoid idling folks as one season ends and another begins–a customary pattern in the San Joaquin Valley.
With that in mind, California Harvesters is actively attempting to sign up several citrus growers, whose fruit will ripen in the winter, so that its workers can move seamlessly from grapes to oranges, lemons, and tangerines. Longer term, Gomez expects others types of work, such as landscaping, to help fill the gaps.
Finally, California Harvesters must continue to establish its credibility with workers. Even though word is out about the company, some are skeptical that being a farm laborer will ever really be decent, much less desirable. After all, others have made promises in the past, with little to show for it in the end.
“They’ve heard it all before,” says Jenny Ramirez, the HR director.
The difference this time is that, after barely a few months, change is actually taking root.
(9)