How constructing data Modeling Saved One university $10 Million
Mo money, mo problems.
June 23, 2015
In most architectural tasks, budgets a long way exceed projections. The japanese span of the San Francisco Bay Bridge notoriously price $5 billion extra than projected and a brand new transit hub near the sector trade heart in new york is in a similar fashion billions over funds. those are just two excessive-profile scenarios. whereas the sources of value overruns range from mission to challenge, expertise can help alleviate one of the reasons. in the case of the lately accomplished Collaborative life Sciences constructing (CLSB) in Portland, Oregon, constructing data Modeling (BIM) device and digital collaboration instruments saved an remarkable $10 million in construction costs on the general $295 million finances. The deft use of those applications helped the design nab an honorable point out within the AIA tap (technology in Architectural apply) Innovation Awards.
The 650,000-square-foot CLSB is a joint mission of the Oregon well being & Science college, Oregon State college, and Portland State university. The three establishments banded together to accommodate their existence sciences packages under one roof to give college students and researchers extra alternatives for collaboration. positioned on OHSU’s new Schnitzer Campus, in Portland’s South Waterfront District, the constructing consists of lecture rooms, lecture halls, research laboratories, retail, and parking. CO Architects served because the project’s design architect and SERA served as govt architects.
“there are numerous issues that may cause a venture to head over price range, from a misalignment of the brief and design aspirations with the on hand price range, to unexpected site conditions,” Alene Davis, an associate foremost at SERA Architects, says in an interview. “From a tool standpoint, complicated geometric designs can be budget-dangerous if there’s no longer a simple technique to keep up a correspondence the specified geometries to the subcontractors in an effort to be building them. BIM helps out enormously on this appreciate.”
BIM In A Nutshell
BIM device helps architects no longer simplest design and construct in three dimensions, but to even have a three-D variation with layers of details about the person components that compose a construction and how they work together in a device. bring to mind it as laptop-aided design (CAD) on steroids. as an instance, if the architects, engineers, or builders need to alternate an element of the design, they can see the ripple results in an instant—how it will impact general cost, if something else in the design wants to vary as a result, and how this is able to have an effect on overall constructing efficiency and construction time. additionally, all of this information is saved in order that at any time all through the lifecycle of the constructing, somebody can go in and establish what components had been used. If something breaks, the manufacturer, version quantity, and other important points are saved so there isn’t a guesswork accomplished in changing it.
These packages were around for many years, however now they’re extra subtle and used extra broadly. Davis likens the rise in BIM to the shift from hand drawings to CAD. Most massive-scale architectural projects contain some combination of BIM modeling and CAD, however each the design and construction groups and all subcontractors for the CLSB used an all-BIM course of—a rarity. “while architects are early adopters of three-D expertise, to demand that all of our contributing consultants use it, and for the contractor to demand that each one of their subcontractors use it’s uncommon,” Davis says, noting that her firm has been the usage of BIM because 2006. “CLSB is without doubt one of the few projects that has accomplished that.”
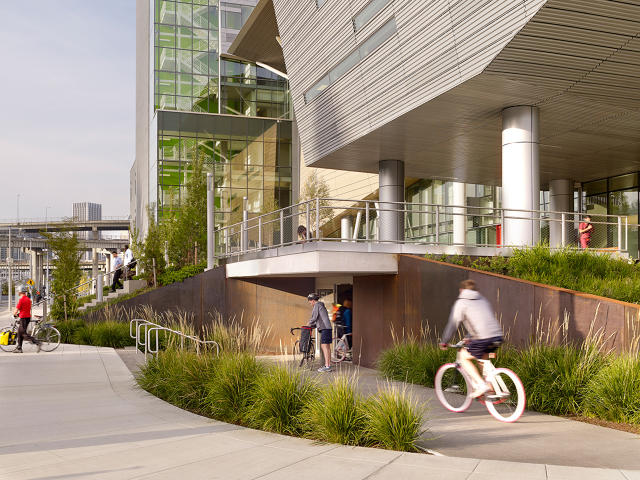
how to save $10 Million
The CLSB concerned 28 totally different design teams, which is standard for a project of this scale. This incorporated the whole thing from civil engineers, landscape architects, roofing consultants, building code consultants, signage design—the record goes on. To make verbal exchange extra environment friendly, SERA Architects and JE Dunn construction used an all-digital documentation process. the firms credit score this move on my own for saving $10 million.
The nitty gritty of the fee financial savings boils all the way down to how 3-D modeling with applications like Revit with the aid of AutoCAD, and Naviswork by means of Autodesk, helped the completely different entities keep in touch higher in the course of the process. as an example, if the architecture firm designed a undeniable function in three-D, that file might then be transferred to the structural engineer after which to the fabricator. “This makes for greater-quality paperwork and reduces conflicts all over construction,” Davis says.
for example, BIM helped resolve potential development conflicts involving positioning of plumbing, electrical, and air flow techniques. A separate team is liable for designing each community. in the 3-d edition, the groups found out that a pipe intersected with a vent [Editor’s note: see slide seven above]. that’s something the clash-detection characteristic of the edition identified sooner than building started out—when adjustments had been moderately straightforward. The plumbing people had been then in a position to design the pipe to wrap around the vent. problem solved.
The change was once then mirrored in real time to every design team concerned. instead of the plumbing design group posting their changed document, and each of the 27 other groups desiring to do the identical to their very own copies of the plumbing layouts, everything up to date concurrently. that is simply considered one of many scenarios that know-how mitigated.
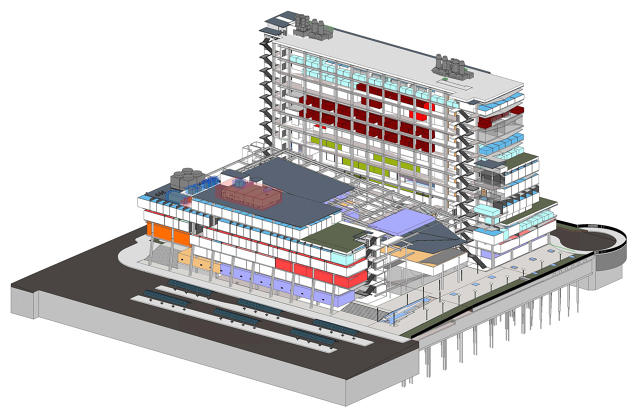
moreover, the design teams used Bluebeam—a collaborative editing and file-sharing platform—to link all the development documents so that one firm’s changes would routinely be reflected in everyone else’s paperwork. Smartsheet, a cloud-based totally spreadsheet answer, also helped the teams preserve track of documents, allowed multiple customers simultaneous get right of entry to and modifying, and prevented model-keep an eye on issues. Posting and drawing documents manually, like development drawings and requests for data, is a laborious undertaking. JE Dunn estimated that it will have taken 127,000 hours to do. At a billable rate of $seventy nine per hour, that is $10,058,017. In paper-related prices alone.
moreover, JE Dunn says that an individual subcontractor who used level layout device, an Autodesk program, and Robotic whole Station, an automated instrument by means of Trimble, to format and install fifty five,000 hangers for the mechanical, engineering, and plumbing systems saved $1 million for the reason that company didn’t must to drill from a raise, insert the hangers, and then have them in my view inspected.
“the usage of an all-digital [design and documentation] process speeded up each coordination and construction,” Davis says. “it can be arduous to determine simply how so much time would have been introduced to the mission if these tactics hadn’t been as streamlined, nevertheless it’s protected to say we saved many months.”
Lesson learned: The machines have won.
fast company , learn Full Story
(199)