How Delta And The Airline Industry Plan To Lose Your Bags Less Often
Anyone who flies on a regular basis is likely to have a luggage horror story, whether it’s a crucial missed connection, a mistaken suitcase, or a bag left on the tarmac as the plane leaves the gate.
If this has happened to you, it might surprise you to learn that the airline industry feels your pain. Reuniting a traveler with a mishandled bag costs about $70 on average, according to Delta, and the industry as a whole lost $2.3 billion to mishandled bags in 2015.
But now carriers are making a major push to keep better tabs on their customers’ baggage. Delta recently spent $50 million on an RFID-based tracking system, which is more reliable than traditional barcodes. And the rest of the industry won’t be far behind: The International Air Transport Association has mandated that all airlines adopt end-to-end baggage tracking by 2018.
Goodbye Bar Codes
Today, most airlines track luggage by printing a bar code, sticking it to the bag, and using laser scanners to send it to its destination. These systems are largely automated, which means they’re prone to the occasional failure, says Bill Lentsch, Delta’s senior vice president of airport customer service and airline operations. From the quality and position of the lasers to the quality of the bag-tag printout, a lot can go wrong as the bag winds through miles of conveyor belts.
“We only get about a 90% read rate on a good day with our current technology of reading the bar codes,” Lentsch tells Fast Company. Bags that fail to scan get pulled from the belt for manual handling, which is how your luggage ends up missing its flight or traveling to the wrong city.
Delta’s new baggage systems rely on radio frequency identification, or RFID. At the ticket counter, Delta prints out a tag with an embedded microchip and antenna, which the airline’s tracking system picks up through radio waves. Instead of requiring a line of sight, RFID can detect bags by proximity.
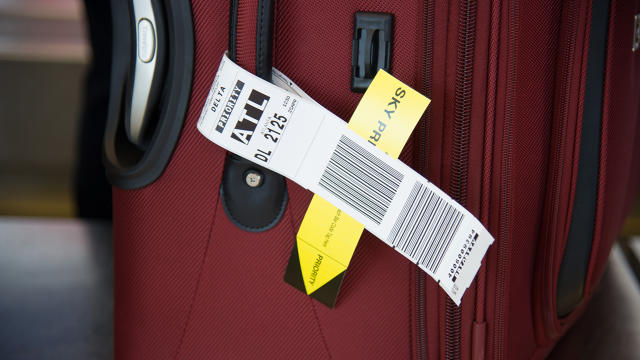
“RFID will give us a 99.9% read rate so that bags move very efficiently through the baggage handling system,” Lentsch says.
RFID also helps out on the tarmac. On each belt loader, scanners detect whether employees are loading bags in the proper order so that the ones with connecting flights come off first. (Lentsch says Delta can retrain those employees if they’re not doing the job right.) And when bags come off the plane, employees can scan them quickly to single out the ones that have tight connections.
“Under a normal process, you’d have to wait for the majority of those bags to come out before we can cut the driver loose and send him over to your departing plane,” Lentsch says.
The technology has a passenger-facing benefit as well: An update this week to Delta’s mobile app lets passengers locate their RFID-equipped bags on a map without having to look up their baggage claim number. Soon users will also get push notifications telling them when their bags have arrived at each leg of the flight. And in those cases where mishandling still occurs, Delta is working on a way to file a claim from the sky.
Delta is now printing RFID tags at all of its airports, and in total it plans to install RFID scanners in 84 airports, which collectively handle 85% to 90% of the airline’s baggage. The other airports, Lentsch says, handle so few bags that manual code scanning is accurate enough. He estimates that the $50 million investment will have paid for itself within about two years.
Return Of RFID
Delta has an early jump in embracing RFID, but it’s not alone. The IATA has been following Delta’s progress, and in a study with SITA—an airline IT group—it estimated that industrywide adoption could reduce mishandling rates by 25% over the next six years, saving more than $3 billion.
“RFID is the easiest way to track bags,” says Andrew Price, IATA’s head of airport operations. “It’s the most cost-effective way for a large number of airlines, not just Delta.”
RFID is not a new technology, and IATA has investigated its potential a couple of times over the past two decades. But those earlier tests only focused on sorting bags into their appropriate destinations, not complete tracking of the bags’ whereabouts.
“We were solving about 20% of the baggage mishandling problem,” Price says. “Our board of governors said, ‘Look, go and solve the other 80% that can be solved without investing in this big technology, and then come back.'”
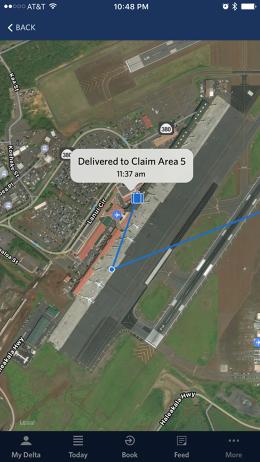
Since 2007, IATA has pushed to reduce mishandling through other means, such as visiting airports to identify systemic problems. Those programs cut down on mishandling by more than 50%, Price says. Today, 99.4% of bags never have a problem.
Now, the trade group is going a step further with a mandate for end-to-end tracking—that is, following a bag from the ticket counter to the airplane, through connecting flights, and back to baggage claim. While airlines can use whatever technology they want under the mandate, IATA is clearly throwing weight behind RFID with its latest business study.
“The reason we’ve put this out now is because it’s been 10 years since we did the last one, and there’s renewed interest in RFID due to the Delta implementation,” Price says.
It probably helps that the cost of RFID tagging has dropped considerably in recent years. Delta’s Bill Lentsch says each RFID bag tag costs about 10¢, which is about twice the cost of a standard bar code printout, but about half the price of RFID five to 10 years ago.
What’s the next step for getting more airlines on board? Price says IATA will release an implementation guide as soon as November, and next year it’ll start offering guidelines for different types of airports.
That said, there’s no penalty if airlines decide to ignore the rules. “We’re going to draw it to their attention, and other airlines will draw it to their attention as well, but we’re an industry body,” Price says. “We’re not a regulator.”
Beyond The Printed Bag Tag
Over the long term, printing out tags with RFID chips on them may not be the only way to improve baggage tracking.
One other possibility involves a permanent bag tag, which would connect to a smartphone via Bluetooth so passengers could transmit their flight information. Customers could then drop off bags without having to get a tag at the check-in counter.
But so far, there’s no industry standard on how these tags should work, or what technology they should use. Qantas, for instance, currently offers bag tags that rely entirely on RFID, while British Airways and Alaska Airlines have experimented with e-paper screens that can refresh with new bar codes.
IATA’s Price says the group is working on a standard for ways that data could be shared with the airlines, but he notes that it’s early days for those efforts.
“We’ve talked about it in the industry a little bit, but it’s way off,” he says. “The idea is that we will make a platform that allows that information to be gathered.”
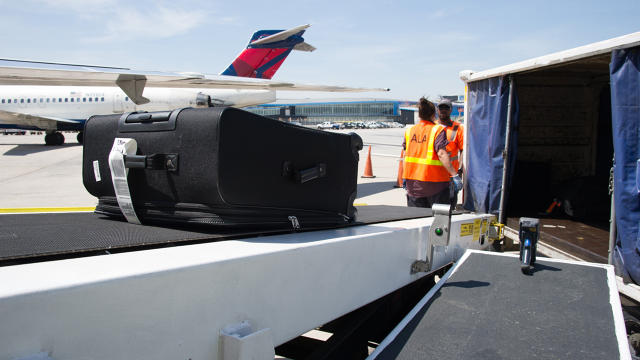
Whatever standard emerges, Lentsch expects Delta’s system to be compliant—in part because Delta is helping to develop it. The work that Delta has done on RFID tracking so far, he says, should support whatever standard emerges later.
“We’re just starting to lay some of the foundation, but another possible expansion here is into the world of permanent bag tags, where you can purchase a permanent bag tag, put it on your bag, and whenever you fly on Delta we’ll be able to read that tag,” he says.
In other words, RFID will likely play an even bigger role in bag tracking, assuming more airlines get on board. And if they don’t, that’s probably good news for Delta.
“While we’re already an industry leader in mishandled bag ratio,” he says, “this is going to put a wider gap between us and our competitors.”
Fast Company , Read Full Story
(45)