throughout the 3-D-Printed Limb manufacturing facility
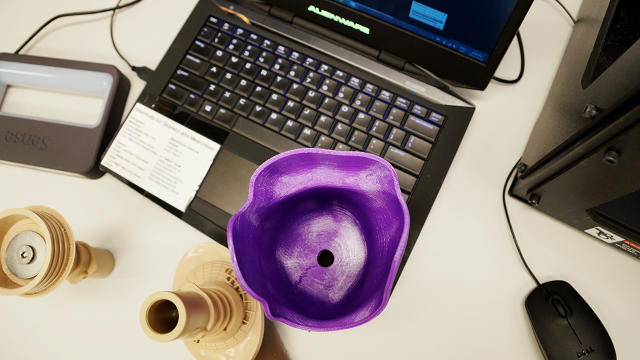
“The social relationships [between] these items matter rather a lot. And these items have got to be created, developed, made to be sustainable as a lot as the tech,” Ratto told fast company in an interview. “if truth be told which you could’t even differentiate, you could’t even separate the tech from the social. they are irretrievably interwoven together. And i think this is the largest drawback with a lot of these tasks, and with know-how more generally.” unlike many different three-D-printed projects, prosthetics do not exist in a vacuum. that you may’t simply add a design to Thingiverse—the well-liked on-line file repository for three-D objects—and expect to change the sector. “i feel some of the things we take as a right after we speak about the availability of technology is that not everybody’s infrastructure is our infrastructure,” says coons.
that’s one of the most realizations that led Rochester Institute of know-how research scientist Jon Schull to discovered e-NABLE, a community of “makers, engineers, scientific professionals, tinkerers, academics, students, artists, philanthropists, [and] folks” that design, customise, and fabricate 3D-printed hand prosthetics for folks with missing or deformed fingers and palms. The gadgets are particularly helpful for youngsters, who are likely to outgrow in any other case pricey industrial prosthetics every few years. Schull says that his team has yes over 3,000 volunteers globally “to collectively work on the fabrication, in addition to the dissemination, of what’s truly a brand new design and distribution channel that complements the existing clinical and commercial channels.” In other phrases, e-NABLE is positioned to work alongside hospitals—most of which aren’t but using 3-D printing in this approach, however nonetheless have traditional prosthetics access and expertise. Some volunteer their 3D printers and printing supplies to fabricate prosthetic hand elements, whereas different teams assemble the parts, and scientific mavens regularly support with guaranteeing the units match and function accurately. In December, Boy and lady Scouts are volunteering to collect palms at John Hopkins hospital. “while we’re doing a lot to make this more straightforward and more uncomplicated for folk to do, there’s no specific reason to suppose that the one that wants this kind of hands will even have the technical abilities required to do design or customise or fabricate or fit this kind of arms,” Schull defined. that’s very much the case in Uganda, the place Ratto and coons are planning to test their ultimate 12 months of labor in a hospital atmosphere. The purpose is to simplify the method of scanning, modeling and printing process without taking out company from health center body of workers. Ratto proven a device wizard written in Python and still underneath development that courses health facility staff through the scanning process with textual content and videos—the usage of what is largely the identical sensor as a primary-technology Microsoft Xbox Kinect—after which throughout the strategy of modeling the prosthetic itself. A clinician can be taught easy methods to customise every prosthetic the use of a bit of tool from undertaking companion Autodesk (called MeshMixer) by using build up the scan in sure areas so as to add relief where areas may well be bonier. Afterwards, they’ll make a negative cast of the scan (all digitally, of course) and prints the prosthetic out.
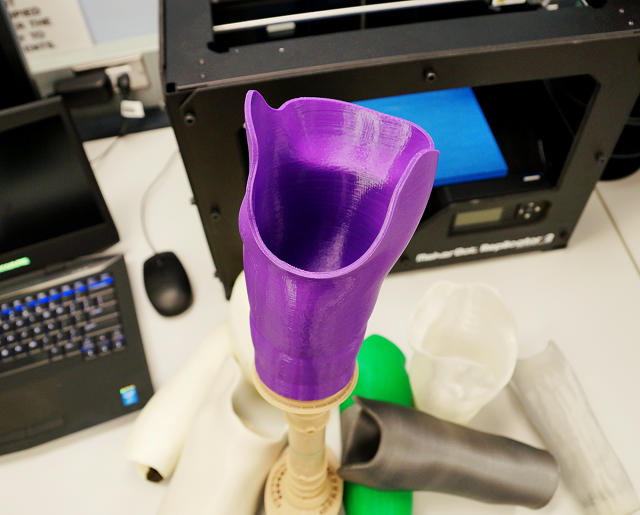
“the simplest manner to do that would be for [the hospital] to ship the scans to us. Or we arrange a provider bureau and we get educated prosthetics from here,” Ratto says. “And it’s a lovely, warm, fuzzy non-profit effort that appears great for lots of Canadian prosthetists. Like, i’m spending my spare time making legs for kids in Uganda,” coons provides. however the issue with that approach is it denies African hospitals the data and expertise to develop these prosthetics themselves. It does not construct new infrastructure, however leverages present networks. the speculation, instead, is to coach and empower—at first, with the aid of setting up CoRSU as a training middle for different hospitals — relatively than make creating nations essentially reliant on international scientific assist. Dr. Albert Chi, who’s an assistant professor of surgical treatment at John Hopkins medication and an e-NABLE volunteer, echoed that view. “We’re having a look not handiest to assist supply places in want but additionally to get them began so they can be impartial,” Chi stated. he is at the moment working to enlarge e-NABLE’s volunteer community overseas. A previous prosthetics project, project Daniel, bills itself as “most definitely the sector’s first 3-D-printing prosthetic lab and coaching facility.” however the work being executed on the vital Making lab is arguably more complicated—particularly, for the reason that decrease-leg prosthetics are load bearing. And Ratto and coons have international plans. The pair hope that, from the time the crew establish their first three-D-printing lab in Uganda subsequent year, as a minimum 65 working prosthetics will probably be printed and sent home with kids over the following twelve months. And all over that time, they’ll be figuring out where and methods to increase subsequent. Ratto and coons recognize that, for this to work they can’t simply installation copycat labs in new hospitals. There will have to be ongoing relationships between every website, the place information and learnings are fed back to the other places and the critical Making Lab’s house base—a network for 3D prosthetic limbs. “the next phase of this work is thinking about how the scaling works. as a result of which you can’t scale out of a research lab. So this idea of a social innovation [or] social entrepreneurship firm is what happens next,” Ratto stated. “and that’s going to be as fascinating as the rest of it, to inform you the reality.” *replace: An prior model of this story incorrectly identified Matt Ratto as an assistant moderately than associate editor. We make an apology for the error.
(151)