Is This Sewing Robot The Future Of Fashion?
Jonathan Zornow got his big idea while watching TV.
The former Seattle software developer has an unusual bedtime addiction: Binging on the Discovery Channel show How It’s Made.
“[The show] just tapes machines doing their thing over and over again,” he says of the educational manufacturing series. “I find it serene, just watching stamps go up and down and the wheels spin around.”
The meditative ritual usually lulled Zornow to sleep, but one episode on blue jeans woke him up. Zornow was stunned to see the complicated steps put into creating a simple pair of pants: The stitching process is still dependent on armies of human laborers.
“It really bothered me,” he recalls. “It seemed strange that we wouldn’t have more automation in that field. I had assumed that robots were making all of our clothes.”
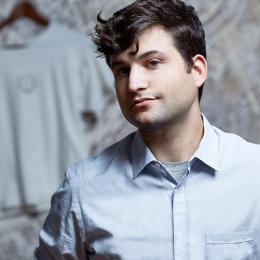
It’s why Zornow came up with Sewbo, a process that chemically stiffens fabrics in order to allow automated sewing robots to produce a full garment. Currently, factories rely on humans to guide fabrics through machines and weave them through assembly lines.
“It seems crazy to me that there was so much labor being spent on these relatively simple goods,” Zornow tells Fast Company. But once I learned more about it . . . clothing manufacturing is pretty complicated, and getting robots involved has been a huge struggle.”
So despite great strides in manufacturing for the automobile and aviation industries in the last few decades, apparel factories remain relatively unchanged. They just moved from the U.S. to the other side of the Pacific where low labor costs helped meet consumer demands for more inexpensive goods. According to a recent study by the United States Fashion Industry Association, 43% of American fashion companies rank rising production or sourcing costs as their greatest or second-greatest business challenge.
While Zornow doubts the U.S. will ever be a net apparel exporter again (“That ship has sailed,” he says), he’s hopeful that at least a portion of manufacturers could return once they recognize automation’s strength.
“I think that automation will be an important tool for the burgeoning reshoring movement by helping domestic factories compete with offshore factories’ lower labor costs,” he says. “When automation becomes a competitive alternative, a big part of its appeal will be how many headaches it relieves for the industry.”
Sewbo is only a year old, but Zornow says he is already fielding dozens of inquiries from overseas factories, where almost all of the clothes on U.S. backs are now made. Domestic apparel manufacturing fell from 50% in 1994 to roughly 3% in 2015, reports the American Apparel & Footwear Association. That means 97% of clothing sold in the U.S. is imported.
How It Works
In the past, companies tried to create complicated mechanical devices to emulate the way a human sews, which “is a very difficult and complicated approach,” explains Zornow. Instead, he took a different tack, manipulating the materials to make them compatible with robots.
He realized that if he stiffened the fabrics by drenching them in liquid polymers, they could be turned into thermoplastic composites and treated like hard materials. And robots need hard materials.
“They’re stiff as a board, but they can be molded: You can apply heat and reshape them, and when they cool down, they’ll hold their shape,” explains Zornow. The machine sews through the stiffened fabric to produce a perfectly finished product. (The process can be used with any sewing machine and most robotic arms, which generally cost about $35,000.) Afterwards, the polymers can be easily washed off with water, no detergent necessary.
There are, however, some limitations. Since the material needs to be completely wet, certain fabrics such as wools or leather are out of the question. But overall, even dry-clean-only goods like silks can go through the process. During a demo, it took roughly 30 minutes for the Sewbo process to complete a T-shirt, but Zornow believes it will take less time once it’s put on a manufacturing assembly line.
“I can say with some confidence that when it goes in the production environment, it will be at the same speed as a human sewer,” he holds. Unlike a human sewer, however, robots do not need breaks and are rarely subject to error.
Even though there has been strong industry interest, Zornow has had difficulty building out a U.S. team. He has yet to make an additional hire because there are so few industrial-scale manufacturing experts in the U.S.
Changing The Industry
Slow progress in the apparel technology sector is something that concerns Whitney Cathcart, founder of Cathcart, a consulting firm focused on automated processes, robotics, and digital innovation.
“Our industry, in terms of manufacturing, is so archaic,” says Cathcart. “You have a lot of people in senior-level executive positions that have been doing the same thing for a long time . . . It’s so common to hear, ‘Well, that’s not how we do things.’”
Cathcart points to the challenges of brick-and-mortar institutions and the underwhelming performance of heavyweights such as Kohl’s and Macy’s during the holiday season. She believes apparel companies failed to adapt to the last decade’s digital revolution: Instead of focusing on how clothing is made, they only focused on improving e-commerce and marketing strategies.
“Maybe people thought the fashion industry was untouchable,” she says, highlighting Amazon’s growing success. “We’re buying differently as a society . . . There are brands you once thought were untouchable that are now going away.”
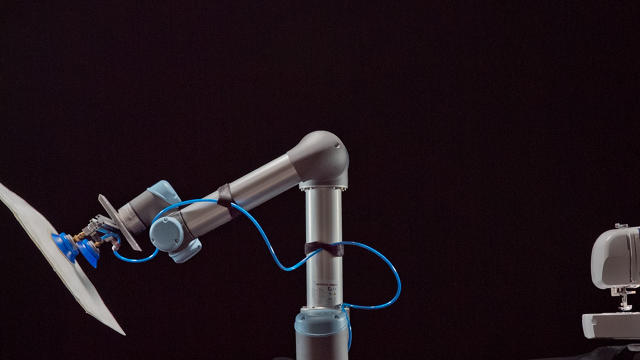
Cathcart was quick to contact Sewbo as soon as she found out about it. In Sewbo, she sees the capability to change how apparel is made. It’s an exciting and lucrative proposition, seeing how sales across the global apparel market are expected to exceed $1.4 trillion in the coming year.
“What he’s creating is completely disruptive,” says Cathcart, who thinks it might help bring automation to factories—and potentially jobs back to the U.S. While the initial investment in robotics seems daunting, Cathcart is confident it will pay for itself over the years, especially as the technology further evolves.
“You look at robots and artificial intelligence, which is still so nascent, and how quickly it’s moved in 24 months, so imagine what it will look like in the next 24 months,” she says of rapid evolvement in the robotics industry. We don’t even know what we don’t know yet.”
It’s a sentiment shared by Zornow, who sees a large opportunity for the U.S. manufacturing community. As of 2016, most manufacturers only have a couple hundred thousand robots deployed. Considering our output, he believes we should have far more.
“This is a big open field for them,” says Zornow. “I think it’s gonna be a land rush to see who can potentially double or more the number of robots they have deployed by getting access to these apparel factories.”
Atnyel Guedj, purchasing manager at global manufacturer Delta Galil Industries, is more skeptical. Having overseen production for numerous labels in various countries across Asia, Europe, and the U.S., Guedj does not foresee apparel manufacturing returning stateside or drastically changing anytime soon.
“I don’t see anyone in the U.S. spending money on expensive machinery,” says Guedj, who sees numerous obstacles in overhauling current industry trends—namely, that apparel production, especially for fast fashion, requires expensive machinery and timely delivery at a very low price. With such challenging margins, companies are forced to seek out the lowest wages possible and are unlikely to invest in new technology. Even China is racing to keep up with increasing outsourcing to Vietnam, Bangladesh, and Ethiopia, says Guedj.
At the same time, Guedj admits that a technological advancement such as Sewbo “is very exciting” and a step in the right direction. At a certain point, he admits, the hunt for cheaper and cheaper labor must come to an end. Technology is the only way out. “[Automation] is the only way forward, and maybe the only way for the industry to save itself from itself,” he says.
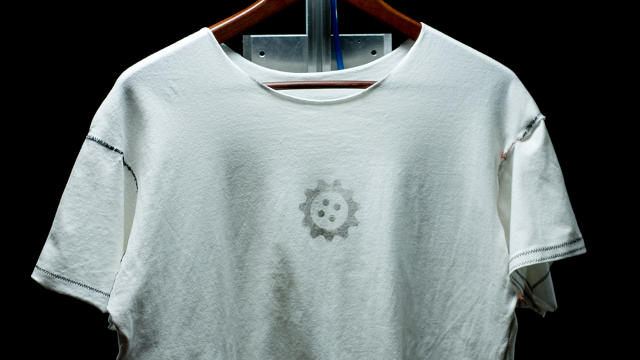
Zornow isn’t naive about the industry’s general distrust of new practices. “It will be a very long time, if ever, before things are 100% automated,” he explains. Fabric production, garment dyeing, and finishing are already highly automated, says Zornow. There is still human labor involved, “but they’re able to leverage machines to achieve incredible productivity, to the point where the labor cost to manufacture a yard of fabric is usually de minimis.”
That is what he hopes Sewbo can do for apparel assembly. The future won’t be entirely run by robots—people are still a necessary component—but factory production can be far more fruitful. “The response has been overwhelming,” says Zornow, adding that the industry “is desperate for automation, and they’re excited about what this could potentially do.”
As he decides his next steps, he’s still loyally watching his favorite show.
“It’s the only thing I’m paying for on Amazon Prime now,” he laughs. “At this point I can call it professional research.”
Fast Company , Read Full Story
(115)