The surprising way this potato chip factory slashed its emissions
November 20, 2024
The surprising way this potato chip factory slashed its emissions
Almost all the emissions from this PepsiCo factory came from heating the oil to fry the chips. A German startup had a solution.
BY Adele Peters
Inside a sprawling PepsiCo factory in the Netherlands that makes more than a million bags of potato chips each day, nearly all the plant’s greenhouse gas emissions come from a single step: frying the chips. The process has always run on a gas boiler. But the factory will soon turn on a new system that can use renewable electricity instead.
The tech, from a German startup called Kraftblock, uses a shipping container filled with small spheres designed to soak up heat. When there’s a lot of cheap solar or wind power available on the grid, the system charges by using the electricity to heat up the material in the container. It can store heat for a few minutes or as long as two weeks, releasing it on demand when a factory needs it.
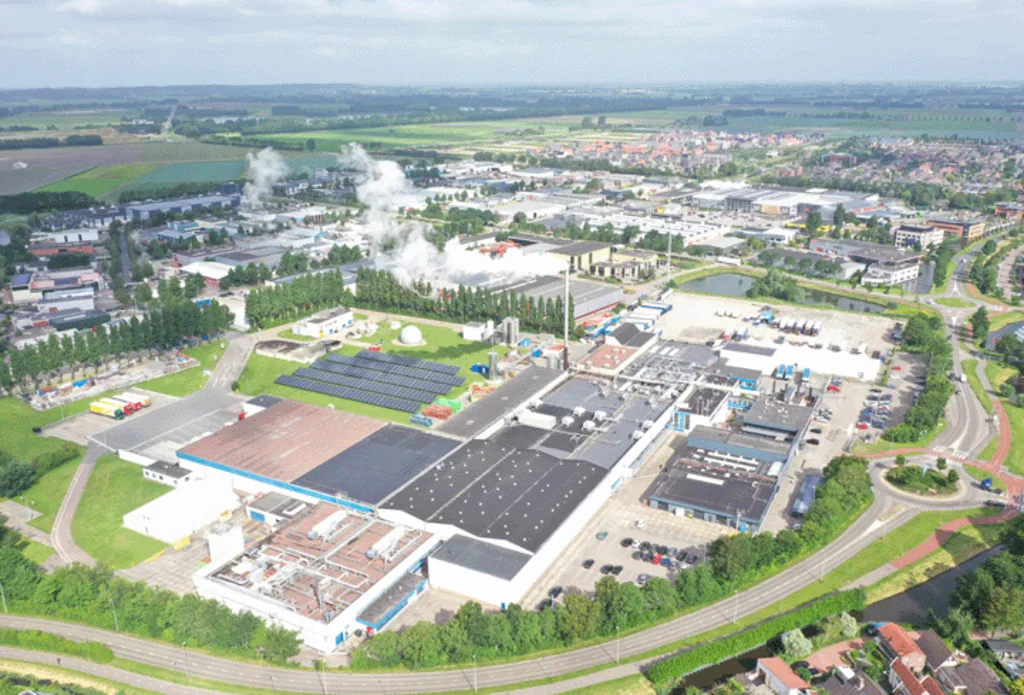
At the PepsiCo factory, the modular new tech will be rolled out in phases. In the first, the tech can cut emissions in half. Making the full switch away from gas can ultimately eliminate 98% of the plant’s emissions—as much as 17,000 tons of CO2 per year.
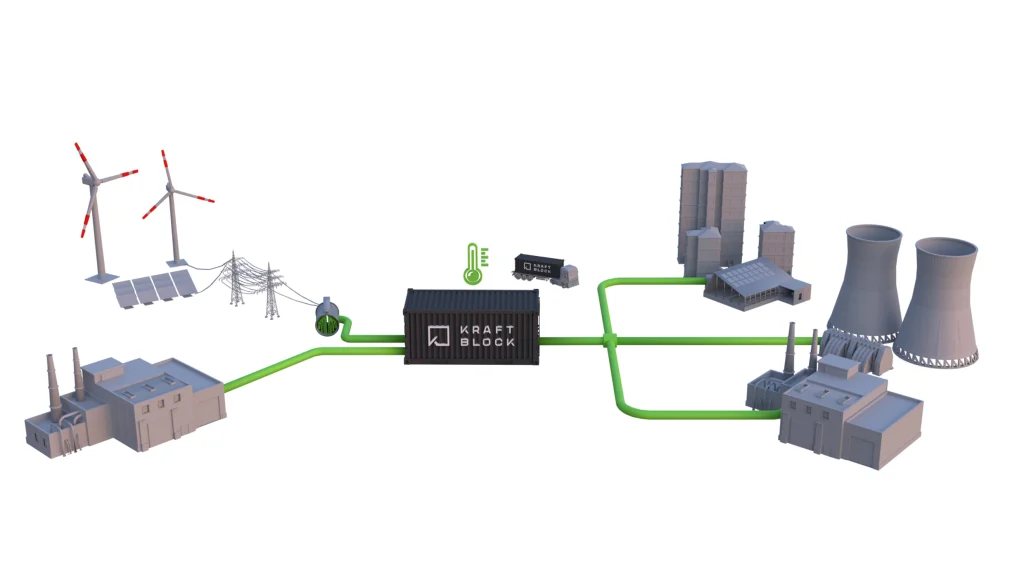
The same tech can be used in any type of factory, from a steel mill to a brewery to a chemical plant. Industrial heat is a major climate polluter, accounting for around 20% of global emissions. “For us, it was a no-brainer to say, if we are able to decarbonize heat generation, we can take a huge step in the race against climate change because we would dramatically reduce carbon dioxide emissions,” says Kraftblock cofounder and CEO Martin Schichtel.
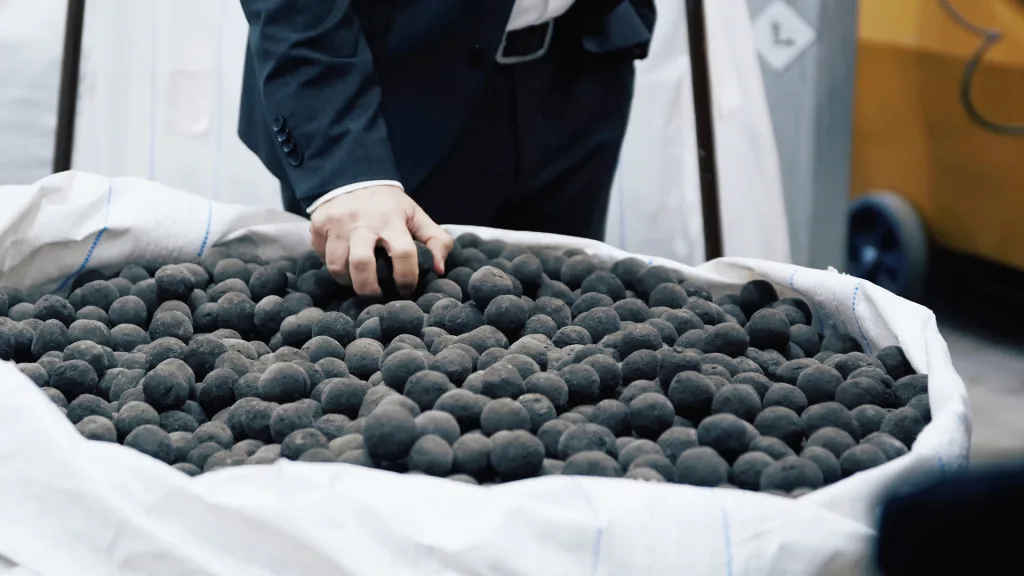
In the past, it has been hard for manufacturers to switch to renewable energy. Factories need a constant source of power (the chip factory runs 24/7, for example) and solar and wind are available intermittently. Factories are often built around fossil-fuel-powered equipment. And the extremely high temperatures needed for some industrial processes can be inefficient to run on electricity.
But Kraftblock’s tech can offer continuous heat, fit in with existing equipment, and provide heat up to 2,500 degrees Fahrenheit. The operating cost is competitive with running on gas, Schichtel says. And factories can typically recover the cost of the initial investment within a couple of years.
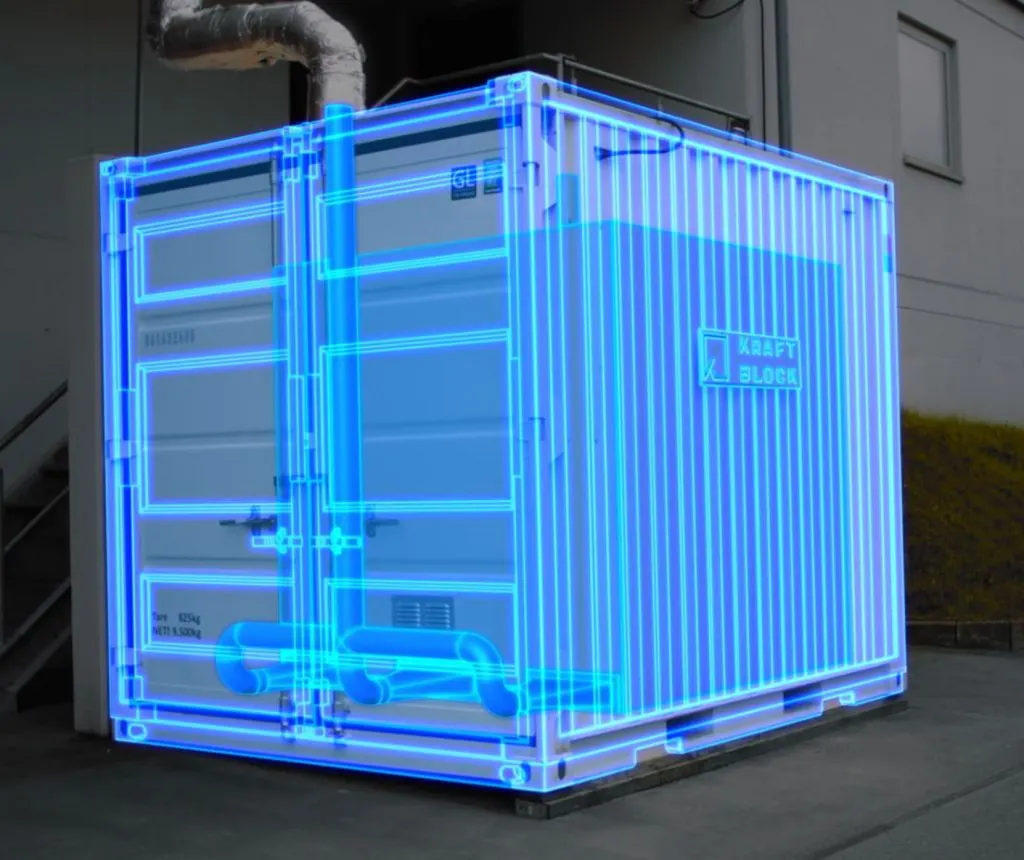
In another project, the company is using waste heat from a ceramics factory to recharge the facility’s storage system. Because its technology can provide more precise heat than the gas system that the factory previously used, the quality of the ceramics is also improving—and the factory has to throw out less waste. Kraftblock is installing systems in multiple other factories, including a steel mill in India.
Startups like Antora Energy and Rondo Energy have developed similar technology, using larger “bricks” to store heat. Kraftblock’s design is a little different, Schichtel says: The spherical shape of its design gives more surface area, so it can absorb and release heat faster. The “pellets” can be made in different sizes (at the Pepsi factory, they’re a little smaller than golf balls) depending on how the factory will use heat. Each pellet is made from recycled materials like steel slag that are ground up into a powder and then held together with a proprietary binder.
The company produces the tech in Germany, but it’s also beginning to work with partners around the world to license it and produce it themselves. “That means we can scale pretty fast,” Schichtel says. The challenge of shifting energy sources is huge: China alone has more than 6 million manufacturers.
ABOUT THE AUTHOR
Fast Company
(10)