The world’s largest zero-emissions truck is more than two stories tall
In photos, a truck commonly used in mining looks a little like a children’s toy. In person, it’s almost unimaginably huge—between 2 and 3 stories high and more than 50 feet long, capable of hauling 300 metric tons of rocks. If you stand in front of it, your head might reach the center of one wheel.
The standard version of this truck also runs on a massive amount of diesel, with a single vehicle emitting as much climate pollution in a year as 700 cars. Around the world, thousands of these giant vehicles are in use. But a new retrofit can shrink a truck’s emissions to zero. First Mode, an engineering startup, has spent the last several months testing a prototype with the mining giant Anglo American, which now plans to roll out the technology in hundreds of other vehicles.
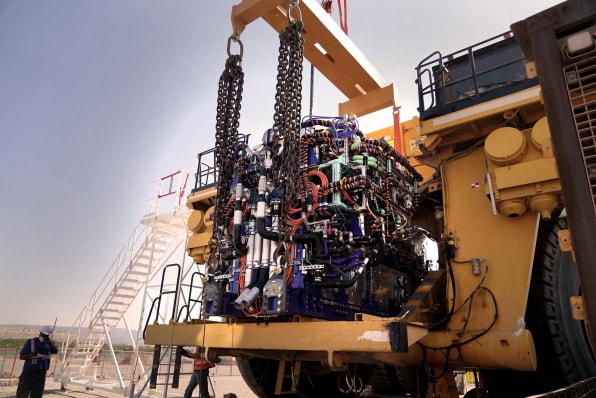
While it’s not hard to build an electric car, the giant size of the truck made it challenging to redesign. “It’s a neighborhood-size power problem,” says cofounder Chris Voorhees. “The vehicles run on around two megawatts of power—that’s about 1,000 to 1,500 homes. So you’re cramming a utility-scale power and energy problem into an off-road vehicle that’s operating in a difficult environment.”
The trucks have to be huge to operate efficiently, says CEO Julian Soles, who joined the company after working on the beginning stages of the project as Anglo American’s head of technology development, mining, and sustainability. Mines choose the size “based on how much material they need to move before they can get to the valuable ore,” he says. Using smaller trucks would also cause traffic jams and other logistical problems. The retrofit had to smoothly fit into existing operations, without compromising performance.
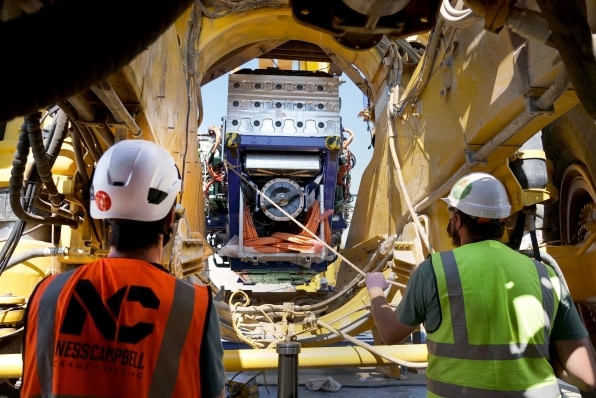
The new design replaces the diesel engine with a combination of a battery and hydrogen fuel cells. It’s not a one-for-one replacement for energy-dense diesel fuel. “Diesel is used because it’s awesome—it’s a great fuel except for that one pesky problem of incrementally destroying the earth,” says Voorhees. While the truck refueled once a day in the past, now it needs to refuel three times in an eight-hour shift (fueling takes about 20 minutes, similar to filling up with diesel). But by tweaking the refueling process, the truck can still transport the same amount of material every day, which is the metric that matters for mining companies.
Pilot tests of the first retrofitted truck started in May 2022 at an Anglo American mine in South Africa, and by the fall, the truck was in regular use. By testing it at an active mine, the engineers got critical feedback, and workers also got more comfortable with the new technology. “Mining is a pretty conservative business, and risk averse,” Voorhees says. “They don’t like to change things. It’s grown organically over hundreds of years. And this is ripping out the circulatory system of the mine and putting in something new.”
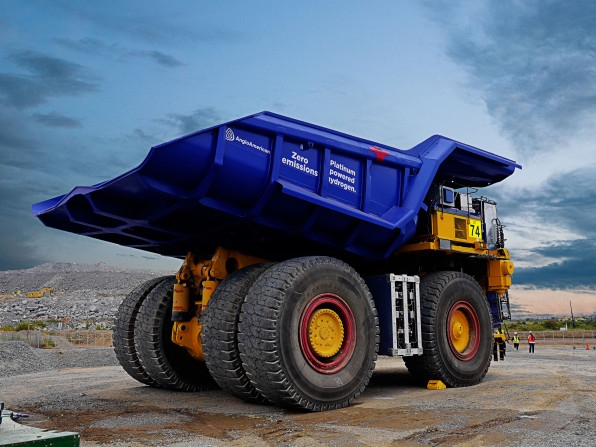
When the company first started working on the design, there were few options for mining companies to decarbonize, he says. But these companies are looking for answers; Anglo American aims to reach net zero emissions by 2040. Trucks are only one part of the problem; crushing and smelting rocks are also major sources of emissions. (And, of course, digging giant holes poses other environmental challenges.) But shifting to hydrogen can make a meaningful difference. Anglo American alone uses nearly 1 billion liters of diesel a year (or about a quarter billion gallons), most of that on huge trucks. And mining will have to continue to grow to meet the demand for batteries in EVs and renewable energy.
First Mode is now working with Anglo American to retrofit fleets at seven of its mines, a process that will take more than a decade; each truck will take around four weeks to retrofit. It’s in talks with other mining companies as well. The startup also will help mines set up a supply of green hydrogen made with clean energy (in some cases, producing the hydrogen at the mine itself).
“We need to help the customers with the full solution—you can’t turn up with a hydrogen truck if there’s no hydrogen,” says Soles. “They need to refuel, and so on. So we really take that whole problem . . . we want to help them do the whole flip.”
(44)