This ancient Roman building technique could help cut carbon emissions
A road or bridge made from modern concrete might only last 50 years. But the massive Pantheon building in Rome, made from unreinforced concrete, has been standing for nearly two millennia. And nearby, some ancient concrete aqueducts still deliver water to the city. What made ancient Roman concrete so much more durable?
A new study from researchers at MIT and Harvard University, along with labs in Italy and Switzerland, suggests that an ancient manufacturing technique can create self-healing concrete that naturally fills in cracks. Using a similar process now could help shrink concrete’s massive carbon footprint. “We’re looking to the ancient world as a source of inspiration,” says chemist Admir Masic, an engineering professor at MIT who focuses on sustainable construction materials.
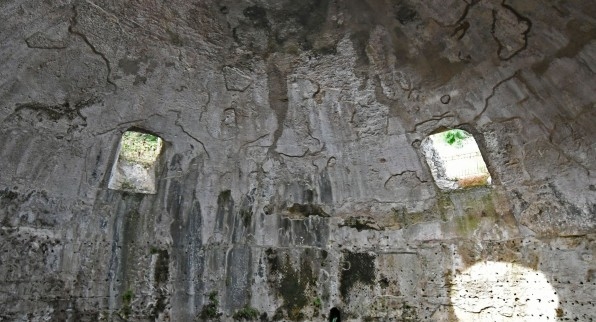
Cement, the glue that binds concrete together, is responsible for up to 8% of global emissions when it’s made, both because of the energy it uses and the process of heating up limestone, a key ingredient in the material, which releases CO2 directly. Multiple startups are now working on alternatives: including companies that replace limestone with different rocks or add captured CO2 to the final product. The Roman-inspired approach is different. By making concrete last much longer, far less of it would need to be made in the first place. (Of course, there’s a catch—we’d also have to make structures that won’t get torn down for other reasons, something that might be harder to know in the age of big box stores.) The older production method also happens at a lower temperature, so it uses less energy.
The researchers studied samples from a 2,000-year-old city wall in an Italian city. They focused on tiny white fragments of lime that aren’t found in modern concrete, but are ubiquitous in old ruins throughout the former Roman Empire. “These are white inclusions that you would find everywhere from the U.K. to Israel and North Africa,” Masic says.
In the past, some researchers thought that the fragments, called lime clasts, were the result of sloppy mixing. But it’s more likely that they were formed deliberately, and the study suggests that they are the reason the concrete lasts so long. When tiny cracks form in the concrete, water travels to the lime clasts, which dissolve and then fill the cracks with calcium carbonate.
The researchers attempted to duplicate the manufacturing process that created the lime clasts, and then tested the material against samples made with modern techniques. After cracking the samples and adding rainwater, they watched what happened: The old-school concrete healed itself within two weeks, while in the modern version, the cracks remained.
Other approaches to “self-healing” concrete also exist now. For example, it’s possible to embed bacteria in concrete that can fill cracks; but it’s costly to make. “Current self healing concretes are very expensive because they are based on very complex chemistry, while our material is super cheap,” Masic says. “It opens the opportunity to build infrastructure that is self-healing infrastructure.” The ancient process involves adding quicklime, a calcium oxide-based material (also known as lime), directly to other ingredients before adding water.
A new startup is now spinning out from the research to bring the concrete to market. It may later add other features that the lab is studying, including making concrete that can absorb CO2 as it sits outside.
(19)