This awesome, Greener Supercar Comes Out Of A three-D Printer
At Divergent Microfactories, constructing a automotive chassis appears to be like just a little like playing with tremendous-strong Tinkertoys.
August 10, 2015
recall to mind air pollution from cars, and you almost certainly think about gas or diesel exhaust. but manufacturing a car, on my own, can add up to a good larger carbon footprint than years of using around. So one startup is taking a brand new option to building a greener automobile: instead of focusing on tailpipe emissions, they’re radically rethinking what occurs in the factory.
within the Divergent Microfactories lab, constructing a car chassis appears to be like a little bit like taking part in with super-sturdy Tinkertoys. the corporate has pioneered the usage of 3-D-printed nodes to connect carbon fiber tubes and panels, a course of that offers manufacturers new flexibility to speedy redesign vehicles—and dramatically reduces the vitality and materials needed to make them.
“If there’s ever going to be a transformation in the car business, it has initially how car chassis are built,” says Divergent Microfactories CEO Kevin Czinger. “Chassis manufacture is where the actual materials, vitality, and capital are invested.”
constructing a standard automobile includes large equipment and bulky, heavy, energy-intensive supplies. “think about the energy wanted to take a a massive coil of steel which gets shipped someplace, lower that metal, put it on a line, and stamp that metal with a stamping laptop,” Czinger says. “At Tesla’s manufacturing facility, they have 5-story tall machines to stamp aluminum. Then it all needs to be welded collectively. you’ve got all of those inputs, and then the inputs from mining.”
The chassis for Divergent Microfactories new supercar, against this, is modest to assemble—it goes collectively in about 20 minutes—and weighs best around 100 pounds. the 3-D printed nodes can match within a backpack. now not only is the method more vitality-environment friendly, it makes it imaginable for small-scale, low-value automotive factories to emerge almost anyplace.
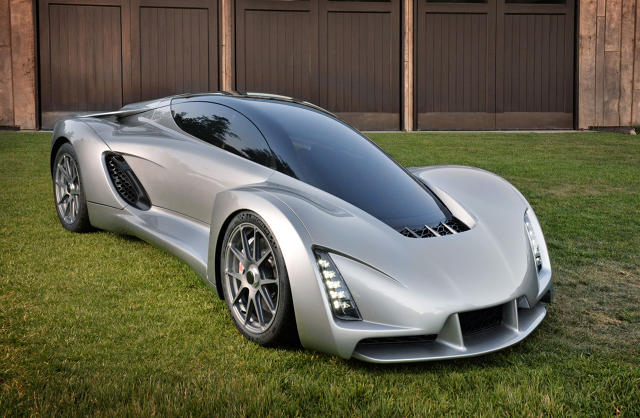
The modular node can easily be tailored into totally different varieties, so producers do not have to invest in the usual complex equipment for each explicit automotive. “once you spend $1 billion for a manufacturing facility, and you’ve got a whole bunch of hundreds of thousands of greenbacks of stamping machines, you’ve gotten frozen your design in time and you might have imprisoned your self in one billion bucks of capital of repeating that design at as excessive a quantity as you can,” says Czinger. With the 3-D printed automotive, a design trade manner changing instrument, not bodily tools.
The startup plans to license its know-how to different automobile producers to help the industry move against flexible, greener future factories. “in the remaining 113 years we constructed about two billion cars,” he says. “as a result of the growing world, in a not up to a 3rd of that time, we’ll construct any other 4 billion. we will triple the collection of cars. The overwhelming majority of that air pollution is going to be manufacturing associated.”
The prototype supercar runs on gasoline or CNG, rather than electricity. the sunshine weight manner it would not need so much gas. When the company crunched the numbers, it realized that adding a heavy electric battery would in truth lower the auto’s total environmental performance. however its chassis machine could simply be used in a Tesla to help make it lighter weight.
“We’re agnostic on drive trains,” says Czinger. “the object about it is there are too many people who are ideological as a substitute of being logical. i’m not in opposition to electrical cars, I just assume you need to look at it holistically, add up the whole influences … but we’re agnostic, and concerned about the chassis. we think that’s the leverage point for getting the business to move in another path.”
[All Photos: via Divergent Microfactories]
(97)