This startup is building a massive indoor farm in a Rust Belt steel town
In a vacant lot next to one of the last remaining steel mills in Braddock, Pennsylvania, a town just south of Pittsburgh, a massive new indoor farm is taking shape. The farm, from a startup called Fifth Season, will begin selling spinach, lettuce, and other leafy greens early next year, using a robot-based system that the founders say is cost-competitive with growing and transporting the same crops from a traditional farm.
It’s more affordable, they argue, than some others in the vertical farming industry. “We looked at vertical farming and realized that the industrywide struggle to make the economics work was a huge factor, and something that would really prevent the industry from truly taking off,” says Austin Webb, cofounder and CEO of Fifth Season, which incubated its first farm at Carnegie Mellon University. “The per-unit economics don’t work. Companies are losing money for every pound that they sell. And that obviously needs to change.”
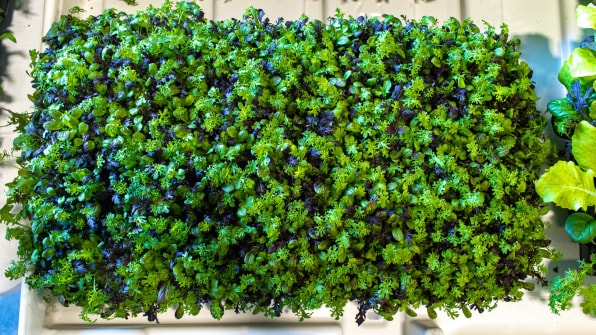
Like others in the space, the startup touts the advantages of growing indoors. It’s possible to use only a tiny fraction of the water that’s used to grow greens in fields; most lettuce is currently grown in drought-prone California and Arizona. (In Arizona, farmers will also soon start losing access to water from the Colorado River.) Growing indoors eliminates the need for pesticides. It eliminates food safety hazards like E. coli contamination. And if crops are grown close to end markets—in this case, restaurants and stores in Pittsburgh—it also eliminates the emissions from trucks traveling thousands of miles and the problem of less-than-fresh produce that may be more likely to be thrown out because it’s already starting to wilt. “When we look at the food distribution system, we looked at it and saw an overly complicated broken system, where no one’s connected to their food, and there’s a lot of food waste,” Webb says.
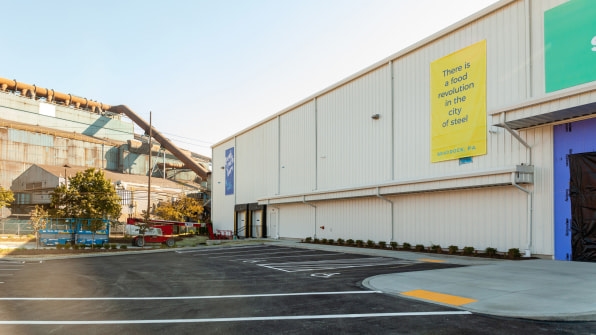
Some past efforts at indoor farming have failed because of high costs, such as FarmedHere, near Chicago, which shut down in 2017 in part because of the cost of labor. “When you look at vertical farms and labor is 40% to 60% of their cost—labor for them is actually more than the all-in delivered cost of Western-grown field produce—it’s just not going to work,” he says. The company’s system, which it has running now at another location and which it’s recreating at the new location, uses around 40 robots. “Together, they’re completely integrated so that our facility is, in a sense, one robotic system.”
Robots plant seeds in trays and deliver trays to grow rooms, where automated systems control everything from the amount of nutrients the plants receive to the schedule of lighting and the amount of carbon dioxide in the air. When a crop is ready, it goes into an automated harvesting system, and then to an automated packaging system, and the trays are sent back to be automatically cleaned and sanitized and then replanted. “We essentially looked at it and said that we should create an automated fulfillment center,” says Webb. “The difference being that instead of pallets of boxes, it should be trays of plants.” Solar panels on the roof and a battery backup system means that the facility can continue operating even if extreme weather takes out the electric grid.
[Photo: courtesy Fifth Season]
Other companies in the industry are also developing automated systems, including Plenty, a Softbank-funded Silicon Valley startup that now has a suite of state-of-the-art custom robotics. Plenty hasn’t shared the details of the cost of its system. But Fifth Season estimates, as an example, that its own robot used for storing and retrieving plants may cost two to three times less. It also uses space more efficiently than some other companies; because everything is automated and humans don’t need to access rows of produce on scissor-lift equipment, the aisles between plants can shrink, growing more produce in the same amount of space. (The new farm is 60,000 square feet, a little smaller than the 69,000-square-foot farm run by another company called Aerofarms.) During its first full year of operation, it expects to grow half a million pounds of greens and herbs, with prices in line with organically grown produce. At that price point, the payback period of the full system will be less than two years.
[Photo: courtesy Fifth Season]
In Braddock, where the population has shrunk more than 90% since its high point in the 1920s to around 2,000 people today, the new farm can provide some new jobs, despite the automation. Three shifts a day will employ 20 workers each. “These are manufacturing-like jobs where we’ve got folks that are helping us operate our machinery,” Webb says. “We’ve got folks that are monitoring the health of the equipment. All of that is something where someone can come from a previous job and you’re not necessarily saying you’re going to do something that’s totally completely different, such as sit at a computer and write code.” As the company expands, it will also hire more engineers and plant scientists.
The startup hopes to replicate the new facility, designed as a modular system, throughout the country. “We’re able to take what we’re building in Braddock and take those blueprints and really hit the repeat button quickly,” he says.
(43)