This Ugandan startup turns plastic waste into construction materials and COVID face shields
The city of Gulu, Uganda, is six hours from the nearest recycling plant—so most plastic bottles collected in that city end up trashed or burned. But in a small pilot facility that’s now operating behind a restaurant in the city’s downtown, a startup called Takataka Plastics is testing a new process to turn plastic waste into something valuable.
The team, led by a PhD student in mechanical engineering from the University of California, Berkeley, created small machines that sort, shred, and melt the plastic so that it can be remade into construction materials and, most recently, reusable, locally made plastic face shields for medical workers who are fighting COVID-19.
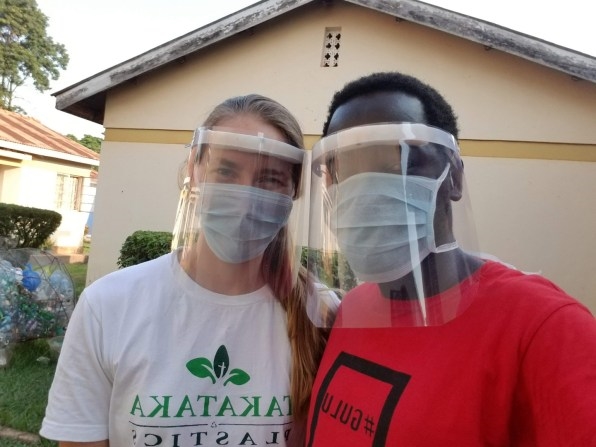
“We’ve designed and built unique equipment for recycling plastic waste because locally built machines are cheaper and easier to maintain and fix if they break,” says founder Paige Balcom. “We based our machines on open-source designs but modified them to use locally available parts and fabrication techniques. If an imported machine breaks, often it cannot be repaired—it’s added to the scrap pile and you’re stuck. We still have to import the electronics, but our locally built machines are also easy to replicate, so we can build many machines less expensively and scale to other parts of Uganda and East Africa.”
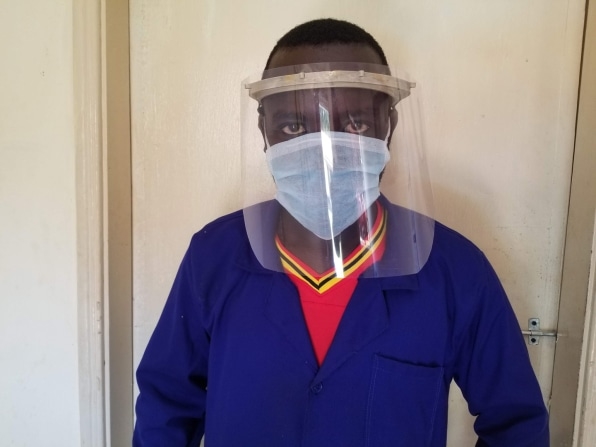
The scale of the challenge is large: Each day, Uganda generates around 600 metric tons of plastic waste. “In Gulu, where we work, 80% of the plastic waste is not collected,” Balcom says. “Instead, most of the plastic is burned, which releases lethal carcinogens and toxins and CO2, or it’s littered anyhow and ends up blocking drains, causing flooding and breeding grounds for malaria-bearing mosquitoes, or it gets into soil and disrupts crops or is ingested by cows.”
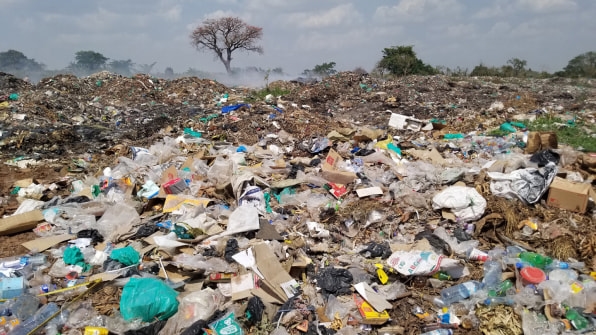
Informal waste collectors can sell plastic waste to recycling companies farther away, in the city of Kampala. But since China and India are no longer buying plastic waste, there’s little demand. “The recycling companies that used to shred the bottles and export the flakes now have nowhere to send all their plastic,” she says. “It’s just piling up and overflowing out of their gates because the water and soda bottles can’t be recycled in Uganda.”
The chemical properties of the plastic make it difficult to process the material for reuse locally, but the startup’s new machinery, engineered to work with the type of plastic found in bottles, makes that feasible. The startup is designing high-value products with the material, beginning last year with wall tiles that are more than twice as strong as ceramic tiles and paving tiles that are more than 14 times stronger than concrete. The construction industry is quickly growing locally, and there’s enough demand for the products that it’s possible to make use of all of the plastic waste.
Before the coronavirus pandemic, the startup collected plastic from the streets, though they now put out collection bins for bottles at restaurants and also collect plastic drip bags from hospitals. The company’s team of 14 people, 6 of whom are formerly homeless youth, is now focused on COVID-19, producing around 100 recycled plastic face shields for health clinics each day.
The overall model can easily expand to other cities and towns where governments can’t afford to build expensive recycling infrastructure, and where it doesn’t make economic sense to deliver waste to a recycling center somewhere else. “After proving our Gulu pilot can be self-sustainable, we want to replicate it and set up Takataka Plastics operations across Uganda and East Africa,” Balcom says. “We’re also exploring the possibility of selling or licensing the designs for our locally made machines.”
(28)