We’re on the verge of making buildings as strong as diamonds
In Neal Stephenson’s 1995 novel, The Diamond Age, he imagines a world in which buildings can be constructed of diamond, a material that, thanks to submicroscopic robots and nanoengineering, had become cheaper than glass. As a result, whole cities are made of the world’s hardest material, and skyscrapers glisten in the sun.
We can’t yet build with unlimited piles of diamond, no. But Rice University researchers have figured out the next best thing: handling plastic, or even materials such as metal and concrete, in a way that can nearly match diamond’s strength.
The findings were just published in the amazingly named academic journal Small. The concept is a bit tricky to grasp, but its implications are easy to understand.
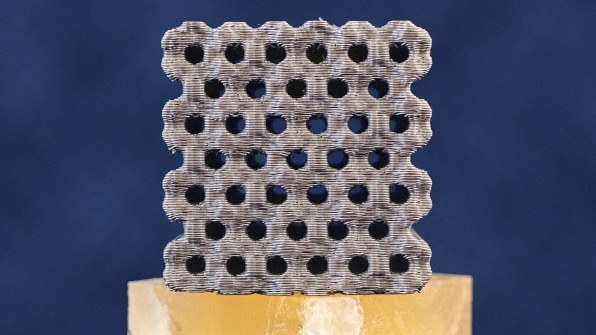
Since the ’90s, scientists have theorized that carbon nanotubes could be arranged in what were dubbed tubulanes. The idea was that if you could arrange carbon molecules in a specific zigzagging mesh structure, you’d get a material that could go blow for blow with diamond.
Scientists did all sorts of simulations on computers, explains lead author Mohammad Sajadi, and at every step of the way, the promise of tubulanes has been proven out. “But nobody can synthesize them,” says Sajadi. “There are lots of theoretical molecular structures . . . but they’re impractical because you can’t make them.” As it happens, carbon nanotubes are a notorious case of theory outweighing application, because the way we make carbon nanotubes today is fairly rudimentary: Baking the right stuff in an oven grows carbon nanotubes that have pretty unpredictable shapes rather than the perfectly organized, molecular geometries of tubulanes.
But instead of trying to make tubulanes in a lab, Sajadi and his collaborators did something different: They copied the woven-looking structure of tubulanes, then 3D printed that shape in a readily available plastic polymer. The shapes were identical but rendered at a scale that was orders of magnitude larger than a tubulane would be.
The finding? Tubulanes and these 3D prints “have the same trend of mechanical properties,” says Sajadi. That means a small block of this printed polymer can literally stop a speeding bullet without shattering or cracking throughout. (A solid cube of the polymer cracked in the same test.) “It shows the role of the geometry is still dominant over the role of material.” In other words, the shape is what’s most important in a building material, not the material itself.
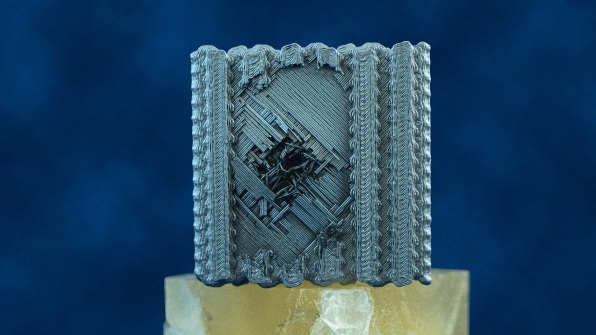
So what is next? Well, perhaps it’s ironic to say, given the previous paragraph, but Sajadi’s lab is experimenting with 3D-printing mock tubulanes out of other materials, such as metal and concrete. So far, the approach is still working. All the tested materials are stronger when printed in these shapes than they were as solid blocks. (And incidentally, Sajadi’s lab is using off-the-shelf 3D printers. You could theoretically do this same experiment at home.)
The implications are wide-ranging. The plastic blocks could be printed in any shape, to make lightweight, bulletproof vests or helmets. They could also work their way into cars. A bumper printed in this way would absorb impact better than the alternatives we have today. If the technique is applied to architecture, Sajadi points out, lighter, stronger brick and walls that can bear more load will allow skyscrapers to reach higher than ever before. (Instead of looking like diamonds, they’d appear more like a gorgeous tapestry of knitted concrete.) At the same time, because these bricks inherently require less material per block, their environmental impact should be lower, too.
“And this doesn’t just have application in building [on earth],” Sajadi offers. “Assume you want a stronger structure in space.”
(31)