Why the primary significant thing To Be three-D Printed In space can be… A Buckle
Editor: Noah Robischon
December 5, 2014
Now that the first functioning three-D printer is on the global space Station, scientists have settled on its first helpful product: A buckle intended to keep astronauts wholesome. Designed through former flight medical professional and astronaut Yvonne Cagle, the buckle is meant to tighten a compression strap that stops muscle loss and keeps heart potential in zero-gravity stipulations—a power challenge for space health. “I turned into very intrigued with what would occur if you need to get the G [gravity] suit and actually used it to recondition the body,” Cagle says. “unless we will print humans, we’ve got to maintain the human physique conditioned so it may function its duties whereas living in space for prolonged sessions of time,” she says.
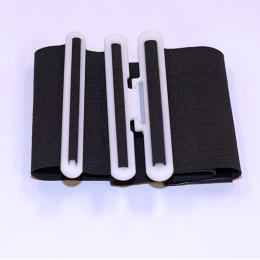
In designing the buckle, Cagle and her group confronted an engineering problem: the right way to make the instrument strong enough to withstand the trials of area flight. “to be able to get there you want something that is going to be a really highly effective stabilizer but has a sufficiently small footprint and is modest enough to repair or print extra if you need it.” Cagle, together with the gap three-D-printing startup Made in house and companions at Singularity college ended up with a simple design that would do something as sophisticated as gauge and test the pressures which can be wanted to recondition the body amidst the atrophying effects of low gravity.
Buckling Up For The body
Designed to be positioned on large muscle groups, the buckle is part of a harness and compression device that astronauts can location any place—a more or less muscle-preserving wearable expertise, says Cagle. sometime subsequent 12 months, it is going to be printed and assembled on the distance station from three separate printed sections, each approximately four.5 inches via one inch. “without the buckle, it’s simply an Ace wrap that is not able to generate better pressures that could protect muscle tissues and nerves,” she says. “The buckle is actually the turnkey to lock collectively the completely different embodiments and design.”
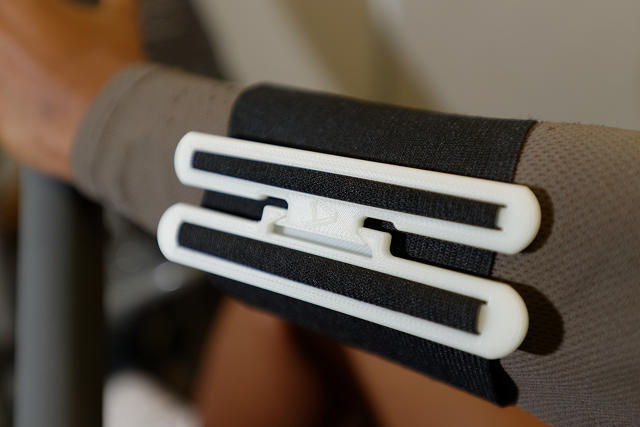
Printing objects in area solves the problem of using light-weight components that could be broken below the stress of a launch—and obviates the need to bring extras from Earth. however Cagle and Autodesk director of strategic initiatives Jonathan Knowles have already began desirous about the buckle’s extra earthly advantages too. “now not simplest can it be used for prolonged-stay space exploration or commercial area, however it can be emailed to folks in the world who’re in mattress leisure or rehabilitating.” The buckle, designed in ]Autodesk’s Fusion 360, might be printed on Made in space’s 2nd technology printer, so that they can be completed in the 2nd quarter of 2015. The California-based totally firm made history when its 3-D printer reached the gap station in September. It printed its first off-world piece closing week, a typical white plastic section emblazoned with the words “NASA” and “Made in space.”
Cagle says she intends to research the info from that initial print to finalize what supplies can be used for the buckle. “Now we know you can put up the design in file time, after which the crew can very promptly and reliably print something that works.” although she’s a former Air drive colonel and astronaut, considered one of Cagle’s probably most vital triumphs used to be as a singer on the world house Orchestra, where she met Knowles, who introduced her to the printing tools. Knowles says he has been exploring area manufacturing design tools for the closing six years and served as an guide to Made in house’s four workers prior to they began the company. Then he changed into its first investor. He and Autodesk have additionally been involved with business projects like the Google Lunar X prize and Moon categorical—the first privately funded company to announce it’ll put a robotic on Mars, someday in 2016. “Our intent is as we glance to establish a everlasting additive manufacturing facility on the ISS, to have this factor Yvonne designed be probably the most first significant things manufactured off-world,” Knowles says.
subsequent: 3-d Printing With Asteroid Stuff
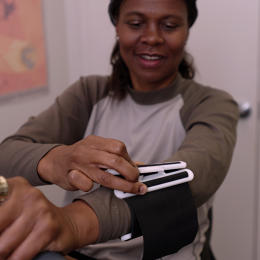
Cagle, Knowles, and Made in area spent the last three years designing the materials and approaches for 3-d printing that would stand up to the G-forces of house. Cagle says she used to be surprised to find the printing process itself made iterating spacewear faster than it is ever been. “using three-D printing, we didn’t have to return to the producer,” Cagle says. “We simply redid the print attempting out completely different designs in a topic of minutes.” though the present printer most effective prints ABS plastic, the following era will be capable to print more materials, including, says Knowles, these mined from an asteroid. “You need to take the next big step in materials if you wish to have an off-world future,” Knowles says. “With one of the vital [materials] patents expiring soon—that are ancient—we will see an explosion in materials [possibilities], so I don’t know what we’ll use.” “It’s a chance to invent new makes use of for outdated materials or old makes use of for new materials that we by no means thought to be ahead of,” says Cagle. different printed objects Cagle desires to design for dwelling in area: an stock tracking device to alert when supplies are working low, first support gadgets like finger splints, and utensils with longer handles—supposed to maintain astronauts and their spacecraft from getting messy all the way through suppertime.
(263)